Struggling with inconsistent colors in your plastic products? Choosing between pigment masterbatch vs raw pigments can optimize your plastic production. Masterbatch ensures consistent colors and eco-friendly processing, while raw pigments offer cost savings for small batches. This guide compares their benefits, costs, and applications to help manufacturers make informed decisions, backed by EuP Egypt’s 17+ years of expertise.
1. What Is Pigment Masterbatch?
Pigment masterbatch is a concentrated blend of pigments or additives mixed into a carrier resin, designed to color plastics. It comes in pellet form, making it easy to handle.
Pigment masterbatch is also known as color masterbatch.
The manufacturing process involves extrusion, where pigments are blended with molten resin, then pelletized for uniform dispersion. This ensures consistent color across plastic products.
Masterbatch is user-friendly, reduces mess, and works well with common polymers like polyethylene (PE), polypropylene (PP), and ABS. Its compatibility and ease make it a go-to for manufacturers seeking reliable polymer colorants or masterbatch pellets.
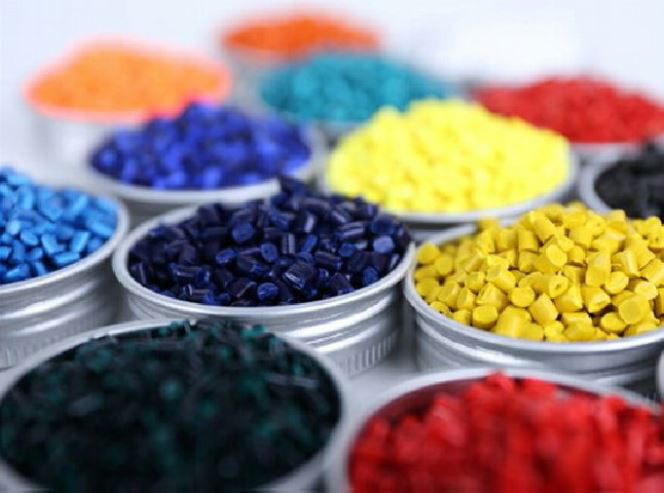
2. What Are Raw Pigments for Plastics?
Raw pigments are dry, powdered colorants used to tint plastic. They can be either organic (bright, vivid colors) or inorganic (more stable, earthy tones). Unlike masterbatch, these pigments aren’t pre-mixed with resin. They’re added manually—either blended with plastic pellets or mixed into a liquid medium before processing.
You’ll often find raw pigments in small-batch production or budget-sensitive projects, where cost is a top concern. But they’re not without issues.
The powder can be messy. It creates dust, which can lead to health risks and factory cleanup headaches. More importantly, getting even color dispersion is tricky. Without proper mixing, the result can be blotchy or inconsistent.

3. What Are Key Differences Between Masterbatch vs Raw Pigments?
When it comes to plastic coloring, both pigment masterbatch and raw pigments get the job done—but they do it very differently.
Form is the most obvious difference. Masterbatch comes in small, dust-free pellets. Raw pigments are powders that can easily get airborne during handling.
Dispersion is another key point. Masterbatch is pre-dispersed in a carrier resin, so it blends smoothly into the plastic. Raw pigments, on the other hand, need to be mixed manually. That means more work—and more room for error.
In terms of handling, masterbatch is clean and easy. No mess, no health risks from floating pigment dust. Raw pigments? Not so much. They can create a messy work environment if not handled carefully.
Finally, there’s compatibility. Masterbatch is typically made to match specific polymers like PE, PP, or ABS. Raw pigments are more universal, but that doesn’t guarantee good results across all materials.
Here’s a quick side-by-side:
Feature | Pigment Masterbatch | Raw Pigments |
Form | Pellets | Powder |
Dispersion | Pre-dispersed | Manual mixing required |
Handling | Clean, dust-free | Can be dusty and messy |
Color Uniformity | High | Depends on mixing quality |
Polymer Compatibility | Polymer-specific | More universal, less precise |
In short, if you want consistent color and easier processing, masterbatch is often the better pick. But if cost is your main concern, raw pigments might still have a place.
4. Which Is More Cost-Effective: Masterbatch or Pigments?
Raw pigments typically cost $2–$4 per kg, while pigment masterbatch ranges from $1–$5 per kg, depending on pigment type, concentration, and additives like UV stabilizers.
At first glance, raw pigments appear cheaper, making them attractive for small-scale or budget-sensitive projects. However, upfront costs don’t tell the full story.
Masterbatch offers long-term savings through efficiency and reduced waste. Its pellet form eliminates dust-related losses (up to 5–10% with pigments due to airborne dispersion) and simplifies handling, cutting labor costs by 10–15%.
Pre-dispersed pigments in masterbatch ensure uniform color, reducing batch rejections by 5–12% compared to pigments, which often require manual mixing and risk inconsistent dispersion.
For large-scale production, masterbatch streamlines processes, lowering energy costs by 5–8% due to faster cycle times. A PVC pipe manufacturer in Saudi Arabia, for example, saved 10% on raw material costs by switching to filler masterbatch.
For small batches (<500 kg), raw pigments may be more cost-effective due to lower initial costs and flexibility for custom colors.
However, for high-volume runs (>1 ton), masterbatch’s reduced waste, labor, and rejections make it more economical, potentially saving 15–30% overall. Consider production scale, labor, and quality requirements when choosing.
5. How Do Masterbatch and Pigments Impact Health and Environment?
When it comes to health and safety, pigment masterbatch has a clear edge. It’s dust-free, clean, and easy to handle. That means fewer risks for workers and a cleaner production environment.
Raw pigments, on the other hand, come in powder form. That powder can become airborne, which isn’t just messy—it can be a health hazard if inhaled regularly. Workers may need masks or extra ventilation to stay safe.
On the environmental side, masterbatch also leads the way. Many suppliers now offer biodegradable or eco-friendly masterbatches, made for use in sustainable plastic products. Some pigments are catching up with more environmentally conscious options, but it’s not as widespread.
Whether you’re exporting or serving regulated markets, compliance matters. Both pigments and masterbatch must meet safety standards like FDA and REACH. But masterbatch is often easier to certify, especially when it’s made for food-grade or medical plastics.
If sustainability and workplace safety are priorities, masterbatch is often the smarter, cleaner choice.

6. Applications of Masterbatch and Pigments in Plastics
Pigment masterbatch and raw pigments play distinct roles across diverse plastic applications, catering to both high-volume and specialized needs.
Masterbatch excels in industries requiring precision and scale:
- In packaging, it delivers vibrant colors for food-grade containers, ensuring FDA compliance.
- In automotive, it produces durable, UV-resistant parts like dashboards.
- Medical applications leverage masterbatch for injection-molded syringes, where consistent color and biocompatibility (e.g., ISO 10993 compliance) are critical.
- Consumer electronics rely on masterbatch for sleek, scratch-resistant casings, while blow molding uses it for uniform plastic bottles.
Raw pigments shine in smaller, creative projects. Artisanal 3D printing benefits from raw pigments, allowing custom color blends for unique prototypes or small-batch designs.
Emerging trends are shaping colorant choices. The growing demand for compostable plastics, driven by regulations like the EU’s 2025 single-use plastics ban, favors biodegradable masterbatches like EuP Egypt’s BioNext. These ensure vibrant colors in eco-friendly products like compostable cutlery.
Raw pigments are also evolving, with eco-conscious organic options gaining traction in niche markets like sustainable 3D-printed art.
Both masterbatch and pigments remain essential, meeting varied industry needs from medical devices to creative, cost-sensitive projects. Choosing the right colorant depends on application, scale, and sustainability goals.
7. How to Choose the Right Colorant for Plastic Production?
Picking between pigment masterbatch and raw pigments isn’t just about price. It depends on your production needs.
Start by asking yourself a few key questions:
- Are you running large batches every day?
- Do you need consistent color across thousands of products?
- Are you working within tight health or regulatory requirements?
If the answer is yes, masterbatch is likely the better fit. It’s clean, reliable, and made for high-volume, quality-focused production.
But if you’re experimenting with custom colors, working on small batches, or keeping a close eye on costs, raw pigments might be a better match.
Here’s a simple way to think about it:
Situation | Best Choice |
Large-scale production | Masterbatch |
Strict color consistency needed | Masterbatch |
Budget is the top concern | Raw Pigments |
Custom or one-off projects | Raw Pigments |
Regulatory compliance required | Masterbatch |
No one solution fits every case. Your best bet? Choose based on your scale, budget, and end-product expectations.
8. FAQs: Pigment Masterbatch vs. Raw Pigments
What’s the main difference between pigment masterbatch and raw pigments?
Pigment masterbatch comes in pellet form and is pre-mixed with a carrier resin. Raw pigments are loose powders. Masterbatch is cleaner and easier to use, while raw pigments offer more flexibility for small batches.
Is pigment masterbatch more expensive than raw pigments?
Yes, upfront costs are higher for masterbatch. But it can save money over time by reducing waste, improving efficiency, and cutting labor costs.
How can I test if masterbatch works with my plastic?
Get the masterbatch technical data sheet to check its carrier resin, like PE or PP. Mix a small batch at 1–5% ratio. Test with DSC or melt flow index to confirm thermal and flow compatibility. Look for even color and no layering during processing.
Are raw pigments safe for plastic manufacturing?
They can be, but safety depends on proper handling. Raw pigments can create airborne dust, so protective equipment and ventilation are important.
What equipment stops pigment dust hazards?
Use enclosed high-shear mixers with dust collectors. Add OSHA-compliant exhaust ventilation to trap particles. Automated dosing systems cut manual handling, reducing dust exposure by up to 80%.
Can masterbatch be used for all types of plastics?
Most likely, yes. Masterbatch can be tailored to match specific polymers like PE, PP, or ABS. Always check compatibility with your material before use.
How should I store masterbatch and pigments?
Keep the masterbatch sealed in a cool, dry place under 25°C to avoid moisture. Store raw pigments in airtight containers with desiccants to prevent caking, especially for organic types.
9. Why Choose EuP Egypt for Pigment Masterbatch?
EuP Egypt stands out as a global leader in pigment masterbatch, also known as color masterbatch, delivering vibrant, consistent colors for plastics across industries like packaging, automotive, and consumer goods.
With over 17 years of experience, we export to 95+ countries, with a strong focus on Africa. Our color masterbatches ensure superior dispersion, heat stability, and UV resistance, offering eco-friendly, dust-free processing.
Using high-grade pigments and resins, we provide standard, custom, and special-effect colors, such as metallic and fluorescent, tailored to enhance plastic products’ aesthetics and durability.
Case Study: Enhancing Automotive Parts with EuP Egypt’s Color Masterbatch
A leading automotive parts manufacturer in California, USA faced challenges with inconsistent color and high batch rejection rates (up to 20%) in producing PP-based interior trim components. Seeking a reliable solution, they partnered with EuP Egypt in 2024 to implement their high-performance black pigment masterbatch tailored for polypropylene.
EuP Egypt’s black masterbatch, formulated with carbon black pigments and PP-compatible carrier resin, ensured superior dispersion and UV resistance. The manufacturer integrated the masterbatch at a 3% let-down ratio during injection molding, achieving vibrant, consistent colors across thousands of parts. The dust-free pellet form simplified handling, reducing labor time by 12% compared to raw pigments. Rigorous quality testing confirmed compliance with ISO 9001.
The results were significant: batch rejection rates dropped by 15%, saving approximately $50,000 annually in rework costs. Color uniformity improved by 95%, enhancing aesthetic quality and customer satisfaction.
This case study highlights EuP Egypt’s expertise in delivering tailored masterbatch solutions for high-stakes applications like automotive manufacturing, reinforcing their value in large-scale, quality-driven production.
10. Conclusion
Pigment masterbatch offers superior color consistency and eco-friendly processing, ideal for high-volume plastic production. Raw pigments suit small-scale, cost-sensitive projects. For vibrant, durable, and sustainable plastic coloring, masterbatch is often the better choice. EuP Egypt’s high-performance color masterbatches ensure quality and efficiency.
Contact EuP Egypt today for tailored solutions!