Polyethylene bags have become indispensable in packaging, offering unparalleled versatility and cost-effectiveness. Explore the features, types, and applications of polyethylene bags, with the knowledge needed to optimize your packaging choices. Whether you’re a business owner, manufacturer, or consumer, this guide will provide the insights necessary to make the most of polyethylene bags for your operations.

1. What are Polyethylene Bags?
Polyethylene bags are plastic bags made from polyethylene (PE), a flexible and durable plastic material. They can be produced from either primary or recycled PE resin.
Polyethylene bags are thin, lightweight, and incredibly durable, making them resistant to tearing and capable of carrying heavy loads. They also offer excellent resistance to water and chemicals, making them versatile and practical. These bags come in a variety of shapes and sizes, catering to different needs and proving to be extremely handy in everyday life.
Thanks to these advantages, PE bags have become widely used across various industries.
- Their chemical resistance makes them particularly valuable in chemical plants and industrial settings where they are used to safely store and transport chemicals without the risk of leakage. This ensures that harmful substances do not affect the environment or human health.
- In addition, polyethylene bags are commonly used in hospitals and laboratories to store medical waste. The durability and flexibility of polyethylene make it a reliable material for packaging, especially for bulky items.
- Furthermore, PE bags are semi-transparent, providing UV protection, which makes them ideal for storing sensitive materials such as artworks and historical artifacts that need protection from sunlight.
2. Types of Polyethylene Bags
Exploring the different types of polyethylene bags, it’s essential to understand the characteristics of LDPE, HDPE, and LLDPE. Each type offers unique properties that make them suitable for various applications, from flexible and lightweight packaging to durable and strong storage solutions.
2.1. LDPE (Low-Density Polyethylene)
LDPE bags are manufactured from low-density polyethylene (LDPE), a type of plastic characterized by its excessive branching and low density. The loosely packed molecular structure of LDPE results in a highly flexible material. However, this flexibility comes at the expense of tensile strength, making LDPE bags less durable compared to other polyethylene types.
These bags are often used for packaging items that require a certain level of pliability, such as bread bags, grocery bags, and other light-duty packaging. LDPE bags are also highly resistant to moisture, which makes them ideal for protecting goods from humidity and other environmental factors.
2.2. HDPE (High-Density Polyethylene)
HDPE bags are manufactured from high-density polyethylene (HDPE), a type of plastic characterized by its dense molecular structure. The minimal branching of the polymer chains during the polymerization process results in a tightly packed and bonded material. This dense arrangement gives HDPE its rigidity, robustness, and durability.
Due to these properties, HDPE bags are commonly used in applications where strength is essential, such as heavy-duty trash bags, grocery bags, and construction materials. The material’s high strength-to-density ratio also allows these bags to be thin yet incredibly tough, making them both efficient and economical.
2.3. LLDPE (Linear Low-Density Polyethylene)
LLDPE (Linear Low-Density Polyethylene) bags are made from a type of polyethylene that combines the flexibility of LDPE (Low-Density Polyethylene) with the strength of HDPE (High-Density Polyethylene). The “linear” in LLDPE refers to the structure of its polymer chains, which are more linear compared to the highly branched structure of LDPE. This linear structure contributes to its improved strength and durability.
These plastic bags offer a combination of flexibility and strength. Unlike traditional LDPE, LLDPE is made through a different manufacturing process that gives it greater tensile strength and impact resistance. This makes LLDPE bags ideal for applications where both durability and flexibility are required, such as in stretch wrap, agricultural films, and heavy-duty bags. LLDPE bags can stretch without breaking, making them suitable for carrying irregularly shaped or bulky items.
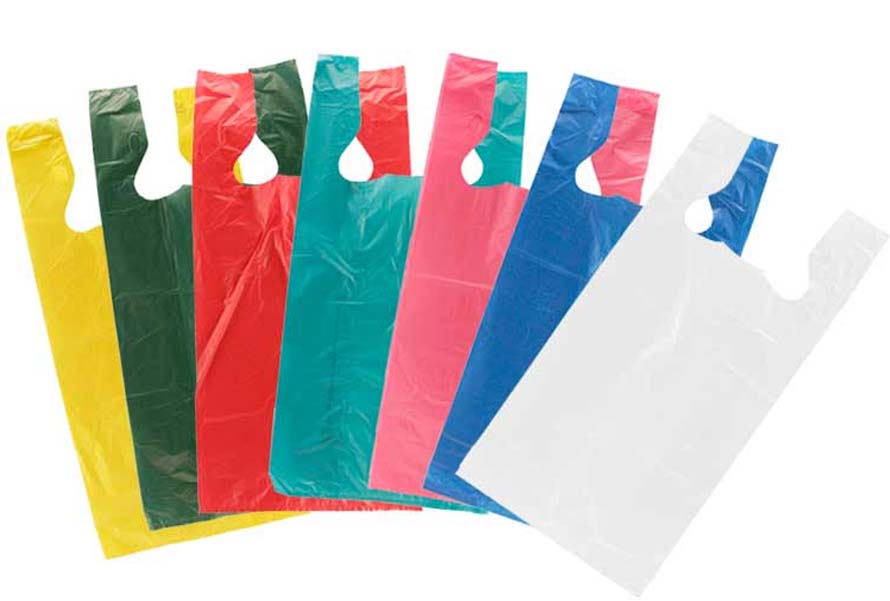
3. Advantages and Disadvantages of Polyethylene Bags
3.1. Advantages of Polyethylene Bags
- Polyethylene bags offer several advantages that have made them a ubiquitous item in modern life.
- Polyethylene bags boast several beneficial characteristics. Although polyethylene is not very strong or hard, it is highly flexible and resistant to impacts; it tends to stretch rather than rupture under stress, making them suitable for carrying a variety of goods, from groceries to clothing.
- Its resistance to water and durability means polyethylene bags last longer when exposed to environmental conditions compared to many other materials, making them convenient for transportation and storage.
- PE bag’s transparent nature allows for easy visibility of the contents within.
- One of the most significant benefits of polyethylene bags is their recyclability. When properly disposed of, polyethylene bags can be recycled into new products, reducing waste and conserving resources.
- Polyethylene bags are cost-effective to produce, making them an affordable option for consumers and businesses alike.
3.2. Disadvantages of Polyethylene Bags
- Despite their numerous advantages, polyethylene bags also pose some environmental concerns. As with other plastics, polyethylene bags can take decades to decompose in landfills, contributing to environmental pollution.
- Incineration, another disposal method, can release harmful greenhouse gases.
- The production of polyethylene bags often relies on fossil fuels like petroleum and natural gas, which are finite resources. The production process itself is energy-intensive and contributes to carbon emissions, exacerbating climate change.
- While polyethylene bags can be recycled, the process can be complex and expensive, limiting their recyclability rate.
- Sorting and cleaning polyethylene bags from other types of plastic is challenging, and the recycled material may not always be suitable for high-quality products.
4. Key Factors When Choosing Polyethylene Bags
When selecting polyethylene bags for your products, it’s essential to consider various factors to ensure optimal product protection and a positive customer experience. Here’s a breakdown of key elements to evaluate:
4.1. Type of Polyethylene
Different types of polyethylene, such as low-density polyethylene (LDPE) and high-density polyethylene (HDPE), have varying properties.
LDPE is generally softer, more flexible, and more transparent, while HDPE is stiffer, stronger, and less transparent. Low-density polyethylene bags are suitable for heavier or sharp-edged items, commonly used for packaging food, hardware, and other substantial products. Besides, high-density bags are frequently used for clothing, small electronics, and other lightweight goods.
4.2. Size and Thickness
Selecting the appropriate size and thickness is crucial for safeguarding your products during handling and storage.
- Size: Choose a bag size that matches the dimensions of your product. For larger or heavier items, opt for a bag that offers more space and durability. Smaller or lighter items may only require a thinner bag.
- Thickness: The thickness of polyethylene bags, measured in mils (one-thousandth of an inch), affects their strength. A 2-mil bag is thinner and less durable compared to a 4-mil bag. Thicker bags provide greater strength but also come at a higher cost, so it’s important to balance durability with budget considerations.
4.3. Customization Options
- Brand recognition: Personalize bags with your logo or message to enhance brand awareness.
- Custom sizes and colors: Tailor the bag dimensions to fit your product precisely. Choose colors that align with your branding to make your bags stand out. Keep in mind that custom bags often involve higher costs and longer production times compared to standard options. However, the benefits in terms of brand impact and customer experience can justify these additional expenses.
- Cost and lead time: Evaluate the additional costs and production time associated with customization.
4.4. Considerations about Environment
If sustainability is a concern, it’s important to consider the environmental impact of polyethylene bags. This includes factors such as recyclability, biodegradability, and the use of recycled materials. Besides, polyethylene bags are not biodegradable and can persist in the environment for hundreds of years. Many businesses are exploring more sustainable options such as biodegradable and compostable bags.

5. FAQs about Polyethylene Bags
5.1. Are polyethylene bags biodegradable?
No, polyethylene bags are not biodegradable. They are made from a synthetic material that takes hundreds of years to decompose in landfills. This contributes to environmental pollution and contributes to the plastic waste crisis.
5.2. Are polyethylene pe bags recyclable?
Yes, polyethylene bags are recyclable, particularly those made from high-density polyethylene (HDPE) and low-density polyethylene (LDPE). The recyclability of PE bags depends on several factors, including the type of PE used, the cleanliness of the bags, and the availability of recycling facilities.
5.3. Are polyethylene bags safe for food?
Yes, polyethylene bags are generally considered safe for food packaging, as they are made from food-grade materials that do not easily leach harmful substances. However, it’s important to ensure that the bags are intended for food packaging and meet all relevant food safety standards.
5.4. Are all plastic bags polyethylene?
No, not all plastic bags are polyethylene. While polyethylene is a common type of plastic used for bags, there are other types of plastic, such as polypropylene, polyester, and polyvinyl chloride, that are also used in bag production. The type of plastic used in a bag will depend on the specific application and desired properties.
Learn more: Most Common Types of Plastic Bags
6. Optimizing Polyethylene Bag Production with PE Filler Masterbatch of EuP Egypt
About PE Filler Masterbatch
PE Filler Masterbatch is a specially formulated blend of high-quality polyethylene resin and other plastic ingredients, such as calcium carbonate or talc. It is designed to enhance the properties of polyethylene resin while reducing costs. By incorporating PE Filler Masterbatch into the polyethylene bag production process, manufacturers can achieve several benefits, including:
- Improved processability: PE Filler Masterbatch can enhance the flowability and processability of polyethylene resin, leading to smoother extrusion and better bag quality.
- Reduced material costs: By replacing a portion of the virgin polyethylene resin with PE Filler Masterbatch, manufacturers can significantly reduce their material costs.
- Improved printability: The addition of PE Filler Masterbatch can enhance the printability of polyethylene bags, allowing for clearer and more vibrant graphics.
- Reduced environmental impact: PE Filler Masterbatch can contribute to a reduced environmental impact by reducing the consumption of virgin polyethylene resin.
EuP Egypt: A Leading PE Filler Masterbatch Supplier
EuP Egypt is a renowned supplier of PE Filler Masterbatch, offering high-quality products tailored to the specific needs of polyethylene bag manufacturers. With years of experience and a commitment to innovation, EuP Egypt has established itself as a trusted partner in the industry.

EuP Egypt is a leading PE Filler Masterbatch supplier
EuP Egypt’s PE Filler Masterbatch products are manufactured using advanced equipment and stringent quality control measures. They are designed to provide exceptional performance and compatibility with various polyethylene resins. By partnering with EuP Egypt, polyethylene bag manufacturers can benefit from:
- High-quality products: EuP Egypt offers a wide range of PE Filler Masterbatch products with customizable properties to meet specific requirements.
- Technical expertise: The company’s experienced team provides technical support and assistance to help manufacturers optimize their production processes.
- Reliable supply: EuP Egypt ensures a consistent and reliable supply of PE Filler Masterbatch to meet the demands of its customers.
- Competitive pricing: EuP Egypt offers competitive pricing on its PE Filler Masterbatch products, helping manufacturers improve their profitability.
By incorporating PE Filler Masterbatch from EuP Egypt into their production processes, polyethylene bag manufacturers can optimize their operations, improve product quality, and reduce costs.
7. Conclusion
In conclusion, polyethylene bags offer a versatile and affordable solution for a wide range of applications. While they have environmental drawbacks, advancements in recycling and the development of sustainable alternatives are helping to address these concerns. By understanding the advantages and disadvantages of polyethylene bags, consumers and businesses can make informed choices that balance convenience and environmental responsibility.
For more information on how to optimize your polyethylene bag production with PE Filler Masterbatch, contact EuP Egypt today.