Melt Flow Rate (MFR) and Melt Flow Index (MFI) measure how easily plastics flow during manufacturing. They guide material selection, quality control, and process optimization for injection molding, extrusion, and blow molding. This guide explains MFR/MFI, testing methods, and practical tips to enhance polymer performance.
1. What is Melt Flow Rate (MFR) / Melt Flow Index (MFI)?
Melt Flow Rate (MFR), also called Melt Flow Index (MFI), measures how easily a thermoplastic polymer flows when melted. Specifically, it tells us how many grams of a thermoplastic polymer pass through a small opening—called a capillary die—in 10 minutes, under set conditions of temperature and pressure.
Think of it like this: you’re heating plastic to a certain temperature, applying a standard weight on top, and watching how much of it flows out in a controlled setup. The more material that comes out, the higher the MFR.
There’s also a related term: Melt Volume-Flow Rate (MVR). While MFR measures mass in grams, MVR measures volume in cubic centimeters per 10 minutes. Both are used to evaluate the flow characteristics of plastics, just in different units.
MFR is closely tied to the viscosity and molecular weight of a polymer. A high MFR means the material flows easily—it has low viscosity and lower molecular weight. On the other hand, a low MFR means the material is thicker, stronger, and flows more slowly. Standards like ASTM D1238 and ISO 1133 ensure consistent testing.
2. How Is Melt Flow Index Tested?
How do we actually measure melt flow rate or melt flow index? The process might sound complex, but it’s fairly straightforward once you understand the setup.
Step 1: Prepare the Sample
The main tool used is called a melt flow indexer (or extrusion plastometer). It’s a machine with a heated barrel, a small die at the bottom, and a piston that applies pressure from the top. The plastic sample—usually in pellet form—is loaded into the barrel and heated to a specific temperature, depending on the type of polymer being tested.
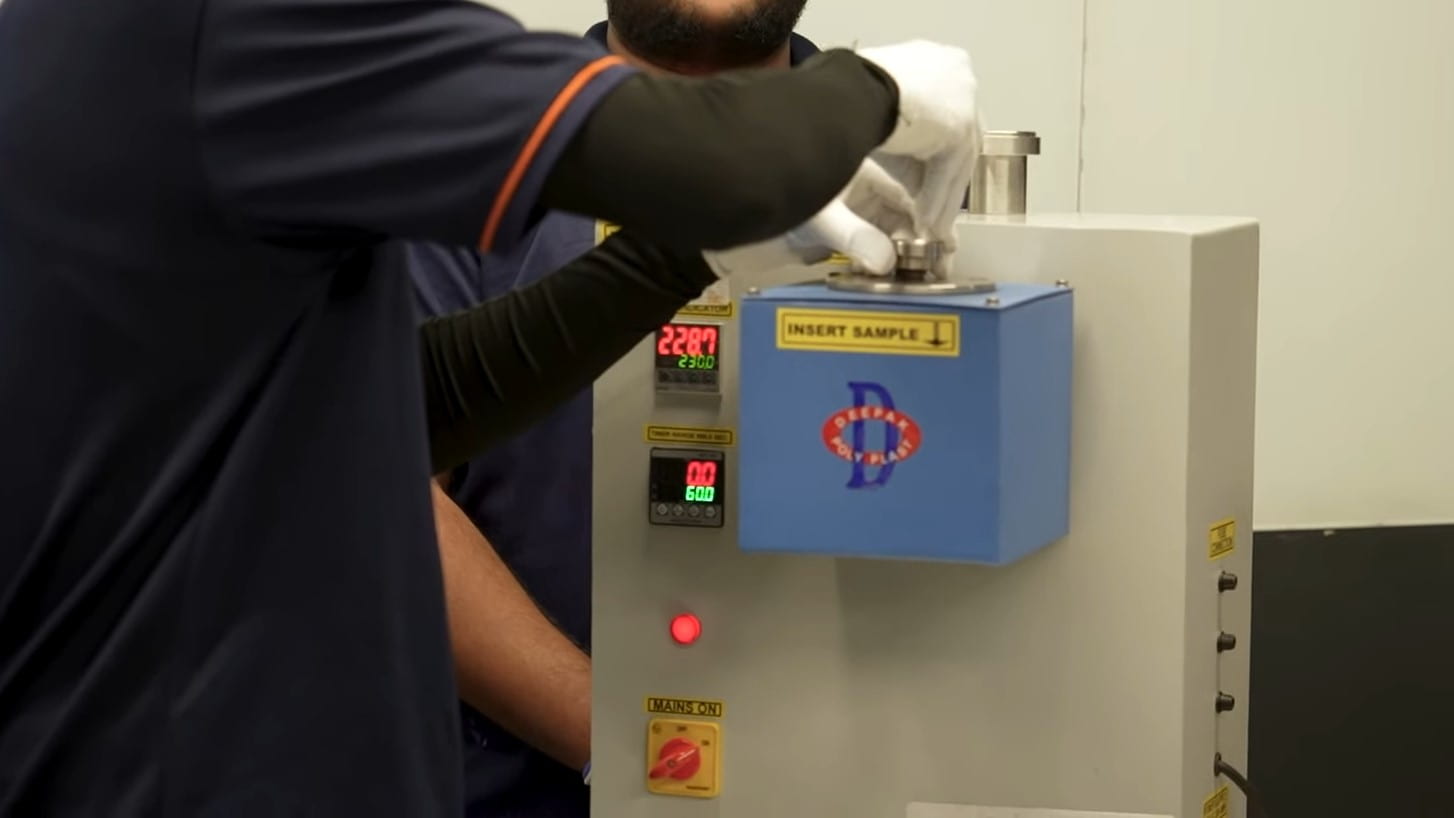
Step 2: Apply Pressure
Once the material melts, a weight (commonly 2.16 kg or 5 kg) is placed on the piston. This pressure pushes the molten plastic through the capillary die. The material that comes out is collected and either weighed or measured, depending on the testing method.

Step 3: Measure Flow
There are two main procedures:
- Procedure A (for MFR): This involves manually cutting and weighing the extruded plastic at timed intervals.
- Procedure B (for MVR): Instead of weighing, this method tracks how far the piston moves using displacement sensors, giving you volume flow.
Accuracy is everything in these tests. Small changes in temperature, load, or die size can skew the results. That’s why standardized test conditions—like those in ASTM D1238 or ISO 1133—are followed strictly.
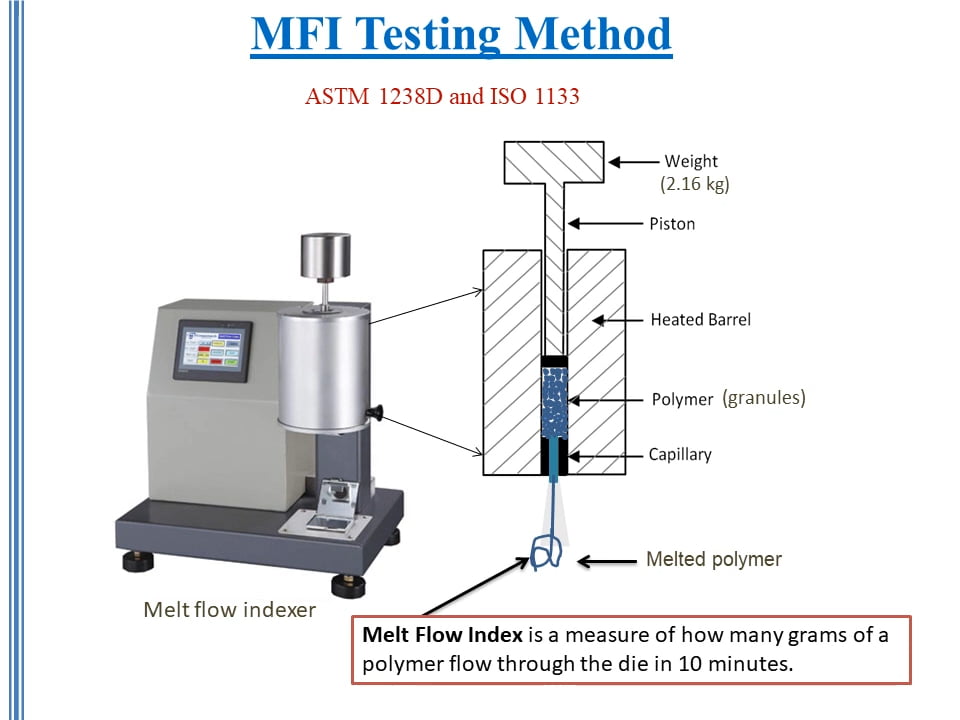
3. Why Melt Flow Rate Is Key to Polymer Processing?
Melt Flow Rate plays a big role in how plastics are processed and how products turn out.
First, it helps with quality control. Manufacturers use MFR to check if each batch of plastic is consistent. If the melt flow rate suddenly changes from one batch to another, it could mean something is off—like a change in material or a processing error. Catching that early can prevent bigger problems down the line.
It also guides material selection. Different manufacturing methods need plastics that flow differently. For example, injection molding often works better with high MFR materials because they flow quickly into complex molds. On the other hand, extrusion or blow molding might need plastics with lower MFRs for more controlled flow.
MFR also affects the final product’s strength. Generally, a low MFR means the plastic has a higher molecular weight, which can lead to better mechanical strength and durability. A high MFR makes the plastic easier to process, but it might trade off some of that strength.
4. Applications of Melt Flow Index in Industry
Melt Flow Index (MFI) is a practical tool that helps manufacturers choose the right material for the right job. Different processes need plastics that flow in different ways, and that’s where MFI comes in.
Let’s start with injection molding. This process pushes molten plastic into detailed molds at high speed. To do that smoothly, the plastic needs to flow easily. That’s why manufacturers often look for materials with a high MFI, usually in the range of 10 to 30 g/10 min. It helps fill complex shapes quickly and evenly.
Then there’s extrusion—used for making pipes, sheets, or films. Here, a steady and controlled flow is key. A moderate MFI, around 1 g/10 min, is ideal for consistent output and smooth surface finishes.
Blow molding, which creates hollow products like bottles, usually needs materials with a low MFI—somewhere between 0.2 and 0.8 g/10 min. This ensures the plastic flows slowly and evenly to form strong, uniform walls.
MFI is also useful when comparing virgin, compounded, and recycled plastics. For example, recycled materials often have a slightly higher MFI due to degradation during previous processing. Checking the MFI helps manufacturers decide if a recycled batch still meets the requirements.
5. What Factors Affect Melt Flow Rate and Index?
Melt Flow Rate can vary a lot depending on the material and how it’s handled. That’s why it’s important to know what affects it—so you can make sense of the numbers and get reliable results.
- Type of polymer: Different plastics melt at different temperatures. (e.g., PE at 190°C, PP at 230°C). These temperature settings can change how easily the material flows.
- Additives and fillers: If you add something like glass fiber or calcium carbonate filler masterbatch, the melt flow rate can drop. That’s because these materials increase the resistance to flow, making the molten plastic thicker and harder to push through the die.
- Moisture: Some plastics absorb water, and even a small amount of moisture can affect test results. If the sample isn’t dried properly, it could flow too easily—or worse, degrade during testing.
- Operator Technique: Inconsistent loading, temperature control, or timing can lead to inconsistent results. That’s why it’s important to follow standard procedures closely.
- Molecular Weight: A wider distribution can lead to unusual flow behavior that a single MFI number might not fully capture.
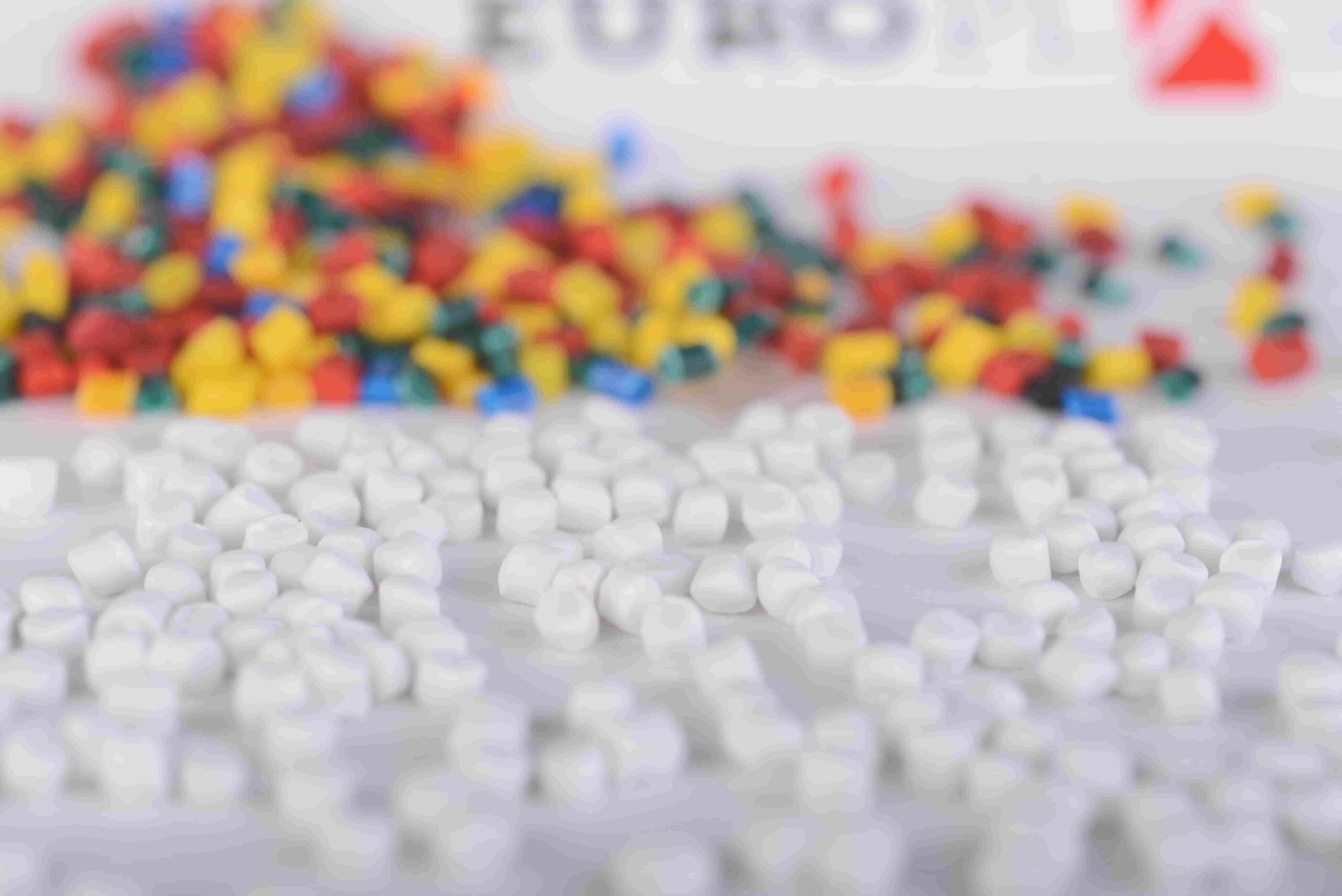
6. Melt Flow Rate vs. Shear Viscosity: Know the Difference
Melt Flow Rate is a useful tool—but it doesn’t tell the whole story. To really understand how a polymer behaves during processing, you also need to look at shear viscosity.
Here’s the difference: MFR (or MFI) gives you a single-point measurement. It tells you how a polymer flows under one specific set of conditions—usually a low shear rate between 7 and 36 s⁻¹. (Note: “s⁻¹” means “per second” and is the unit for shear rate — how fast the material layers move past each other.) But in real-world processing, like injection molding or extrusion, materials often experience much higher shear rates—sometimes over 1000 s⁻¹.
That’s where shear viscosity comes in. It measures how the material flows across a range of shear rates, giving a fuller picture of its behavior under pressure, speed, and heat. This is typically done using capillary rheometers, which are more advanced than standard melt flow indexers.
Another key point: MFI is not a direct measure of viscosity. It’s influenced by viscosity, yes—but also by other factors like molecular structure and additives. That’s why two materials with similar MFI values might behave very differently during processing.
So, for more demanding applications or detailed material studies, combining MFI with rheological testing gives much better insight.
In short, MFR gives you a snapshot. Shear viscosity shows you the full movie.
7. How to Optimize Melt Flow Testing for Accuracy?
Getting reliable melt flow results is not only about using the right machine but also about how you use it. Small mistakes in testing can lead to big problems in production, so it’s worth taking the time to get it right.
- Maintain Equipment: The barrel should be clean, the die should be free of residue, and the piston should move smoothly. Even small bits of leftover plastic or dust can throw off the results. Also, place the machine on a stable surface to avoid vibrations that could affect measurements.
- Calibrate Regularly: Like any precision tool, a melt flow indexer needs regular checks to stay accurate. Follow the manufacturer’s guidelines or testing standards like ASTM D1238 or ISO 1133 for best practices.
- Use Automation: If your lab runs a lot of tests, automated testers can help. Some models (e.g., Yasuda models) can remove operator error and keep everything consistent.
- Record Conditions: When you record results, always note the test conditions: temperature, weight, die size, and procedure type (A or B). Without this info, MFR numbers can’t be compared across batches or labs.
- Control Variables: Use the same operator, test in a stable environment, and prepare samples carefully. Moisture, contamination, or uneven loading can all lead to inaccurate results.
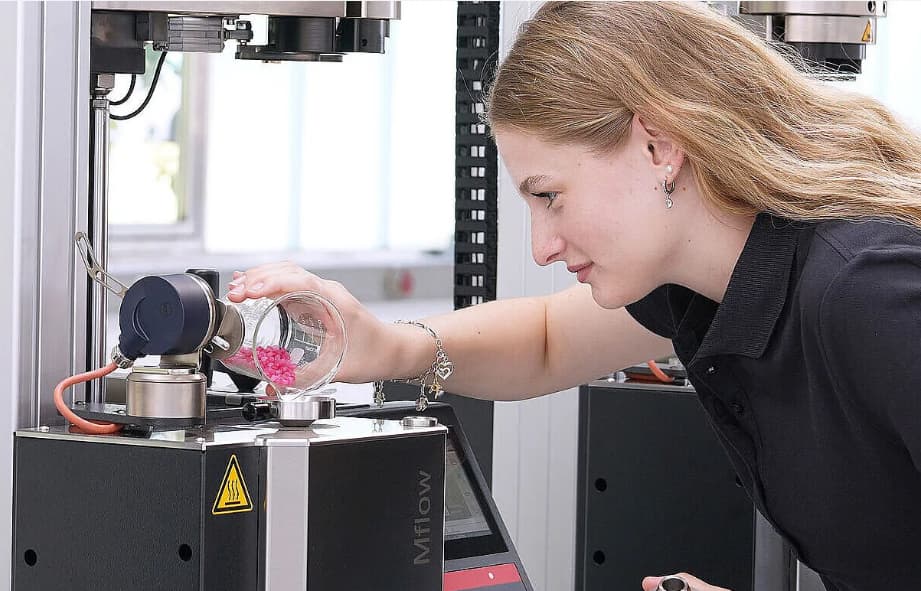
8. Choosing the Right Polymer Based on MFR/MFI
When it comes to selecting a polymer, melt flow rate (or melt flow index) is one of the first things to check. It tells you a lot about how the material will behave during processing—and what kind of product you’ll get in the end.
If you’re working with complex molds or high-speed injection molding, a high MFR polymer is usually the way to go. These materials flow easily and fill detailed shapes quickly, which helps reduce cycle time and energy use.
But there’s a trade-off: higher MFR often means lower mechanical strength. So, if strength or durability is important, you may want to choose something with a lower MFR.
On the flip side, low MFR materials tend to have higher molecular weight. This gives them better toughness, dimensional stability, and resistance to stress over time. They may be a bit harder to process, but they’re a great choice for load-bearing parts or products that need to last.
Here are a few examples:
- Polyethylene (PE): Ranges from 0.2 to 30 g/10 min depending on grade (film, injection, or blow molding).
- Polypropylene (PP): Often 2–12 g/10 min for general applications.
- Acrylonitrile Butadiene Styrene (ABS): Typically lower MFR, offering strength and rigidity for automotive or consumer goods.
Choosing the right MFR isn’t just about flow—it’s about balancing performance, processability, and cost. The better your match, the smoother your production—and the better your product.
Read more: Melt Flow Index of Polymers with Comprehensive MFI Table
9. Advances in Melt Flow Testing Technology
Melt flow testing has come a long way. What used to be a mostly manual process is now more accurate, faster, and easier to manage—thanks to modern technology.
Today’s melt flow indexers often come with microcomputer controls and touch-screen interfaces. These features allow operators to set test conditions more precisely and monitor everything in real time. It also reduces the chances of human error, especially in high-volume labs.
One major upgrade is automated cutting and measurement. Instead of manually slicing and weighing the extruded plastic, some machines do it all for you—automatically collecting data and calculating MFR or MVR on the spot.
There’s also multi-weight testing, which allows users to apply different loads in one session. This gives a broader picture of how the material flows under various conditions and can even hint at the molecular weight distribution of the polymer.
Some advanced models use precision encoders, like those from Baumer, to track piston movement more accurately. This boosts the reliability of MVR measurements, especially for materials with subtle flow differences.
All these improvements help labs get more repeatable, consistent, and detailed data—which means better decisions and better products down the line.
10. Common Standards for Melt Flow Testing
To make sure melt flow data is accurate and comparable across different labs and industries, testing follows strict international standards. These standards define everything—from the test temperature and load to the die dimensions and timing.
The most widely used standard is ASTM D1238. It’s commonly followed in the United States and sets the procedures for measuring MFR and MVR in thermoplastics. This standard covers both Procedure A (for MFR, using manual cut-and-weigh) and Procedure B (for MVR, using piston displacement).
Outside the U.S., many companies follow ISO 1133, which comes in two parts:
- ISO 1133-1 is used for most thermoplastics under standard conditions.
- ISO 1133-2 is tailored for moisture-sensitive materials, like PET or polyamides, which require pre-drying and tighter control during testing.
There’s also ASTM D3364, which focuses on capillary rheometry—a more advanced method for analyzing polymer flow over a wider range of shear rates.
Why do these standards matter? Because without them, two labs could test the same material and get very different results. Following standardized methods ensures everyone is speaking the same language when it comes to melt flow.
11. Practical Tips for Manufacturers Using MFR/MFI Data
Knowing the melt flow rate of your material is useful—but knowing how to use that data is what really makes the difference in manufacturing.
First, use MFR or MFI as an early warning system. If a batch suddenly shows a much higher MFI than expected, it might cause flashing during molding—where excess plastic leaks out of the mold. On the other hand, a batch with too low an MFI might not fill the mold completely, leaving short shots or weak parts. Tracking MFI regularly helps you catch these issues before they turn into waste or customer complaints.
MFI is also a handy tool when working with recycled materials. Recycled plastics can vary from batch to batch. Comparing their MFR to a known standard helps you decide if they’re still usable—or if they need to be blended or modified to match performance needs.
For a fuller picture, combine MFR data with other tests like DSC (Differential Scanning Calorimetry) or TGA (Thermogravimetric Analysis). These give insight into thermal properties and stability, helping you better understand how the material will perform during processing and in the final product.
In short, MFR is more than a number. When used wisely, it can improve product consistency, reduce downtime, and even support sustainability goals by helping you evaluate recycled content with confidence.
12. MFR Ranges for Common Applications
Process | Typical MFR Range (g/10 min) | Notes |
Injection Molding | 10–30 | Fast flow for complex molds |
Extrusion | ~1 | Steady flow for pipes, films |
Blow Molding | 0.2–0.8 | Slow flow for strong walls |
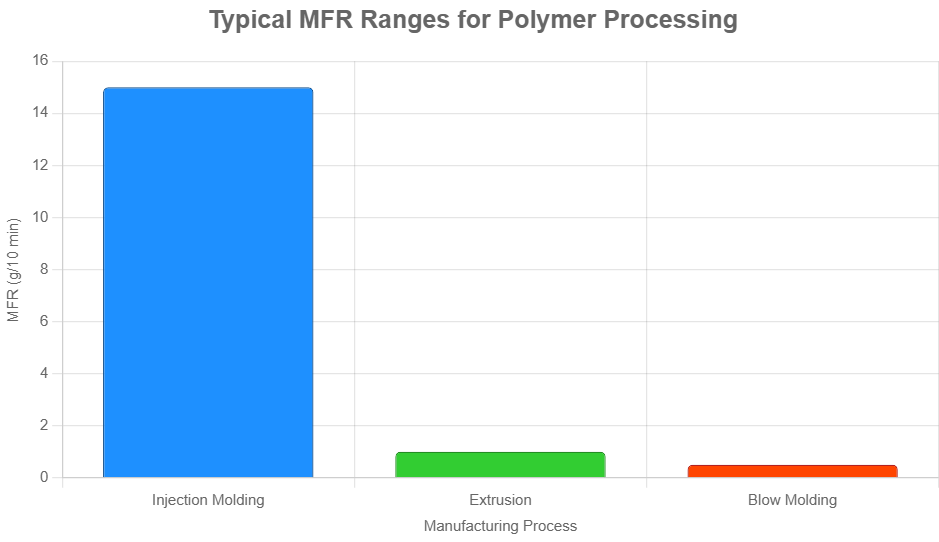
13. Conclusion
Melt Flow Rate and Melt Flow Index are essential tools for evaluating plastic quality and processability. While they don’t tell you everything, they offer valuable insight into how a material will perform—and how it fits into your process.
For best results, understand their limits, follow standard procedures, and use them alongside more detailed tests when needed.
Whether you’re producing bottles, automotive parts, or films—knowing your MFR means knowing your material.
At EuP Egypt, we supply high-quality filler masterbatch solutions that are optimized for consistent melt flow and excellent processability.
If you’re looking for a trusted partner to enhance your polymer performance, contact us today to learn more.
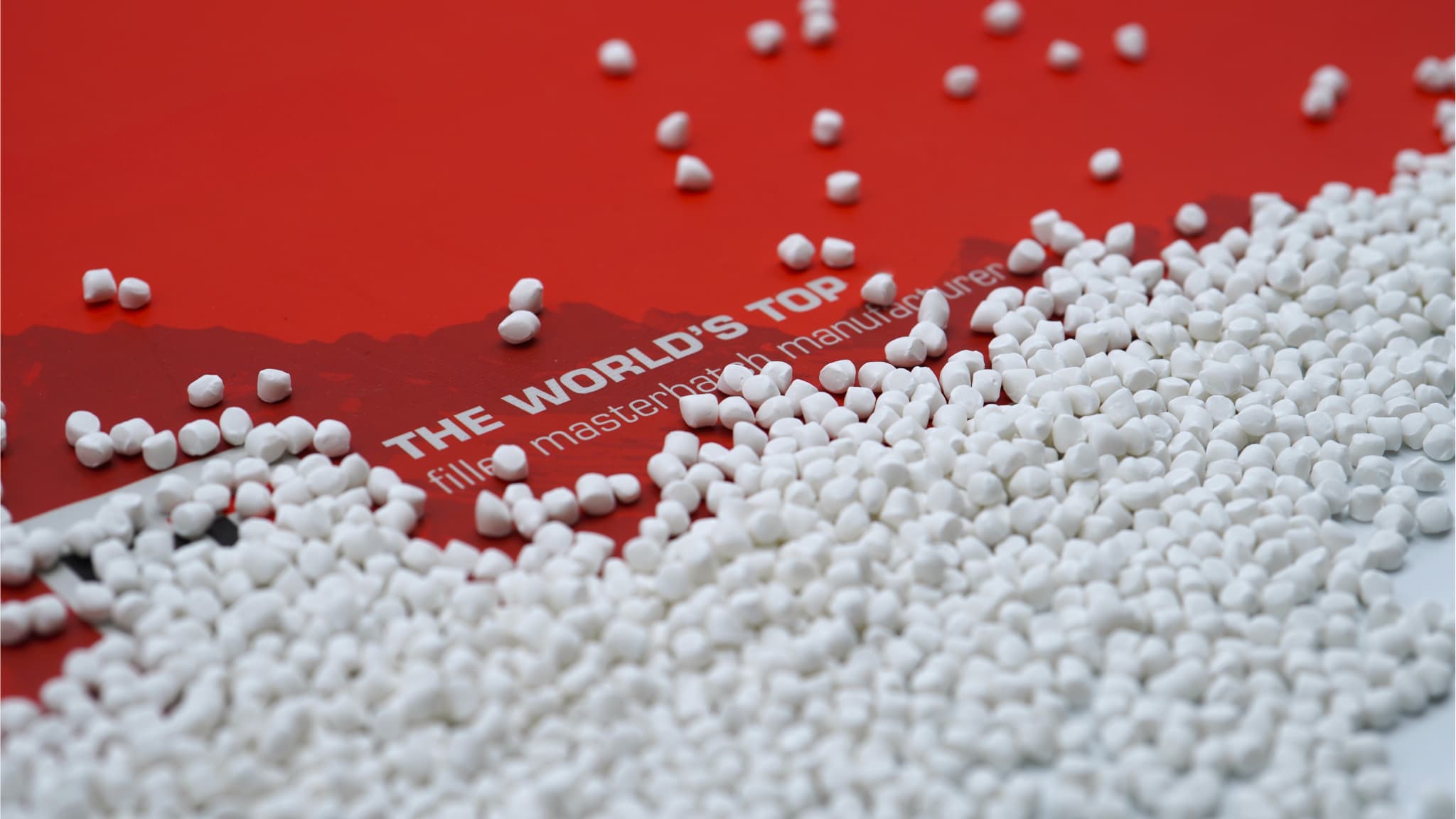
14. FAQs About Melt Flow Rate and Index
Q: What is the difference between MFR and MVR?
A: MFR (Melt Flow Rate) measures the mass of polymer that flows in 10 minutes (in grams), while MVR (Melt Volume-Flow Rate) measures the volume (in cm³) under the same conditions. Both indicate flowability but use different units.
Q: How does MFI relate to polymer molecular weight?
A: Generally, a higher MFI means the polymer has a lower molecular weight and flows more easily. A lower MFI suggests higher molecular weight and better mechanical strength.
Q: What are the standard test conditions for common polymers?
A: It varies. For example, polyethylene (PE) is typically tested at 190°C with 2.16 kg, while polypropylene (PP) is often tested at 230°C with 2.16 kg. Always check ASTM D1238 or ISO 1133 for specifics.
Q: Can MFI be used to predict mechanical properties?
A: Not directly. MFI gives an idea of flow behavior, which loosely relates to molecular weight. But for detailed mechanical data, other tests like tensile strength or impact resistance are needed.
Q: How do additives affect melt flow index?
A: Additives like fillers or fibers often reduce flow, lowering the MFI. Some plasticizers, however, can increase it. Always test each formulation to be sure.
Q: What happens if MFR is too high or low?
A: High MFR may cause flashing; low MFR may lead to incomplete mold filling.
Q: How do additives affect MFI?
A: Fillers lower MFI; plasticizers increase it. Test each formulation.
Q: Can MFI predict production costs?
A: High MFR reduces cycle time but may require costlier additives. Low MFR increases processing time