Finding the right flexible plastic sheet for your specific project is fundamental to success, durability, and efficiency. This article will guide you through the key factors in choosing the right material for each project. Let’s find out right below!
1. Understanding Flexible Plastic Sheets
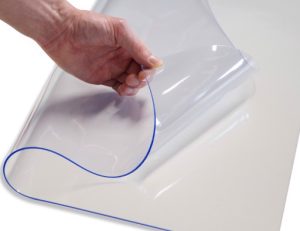
Flexible plastic sheets are thin materials made from a variety of polymer compounds. They are usually in a flexible state and can be bent without breaking. These sheets have become quite popular in many industries today.
Flexible plastic sheets possess many outstanding properties. They are very durable in terms of resistance to abrasion and environmental factors. Thanks to their flexibility, they can be easily cut, shaped and molded into a variety of product designs. They are also light, moisture-resistant and cost-effective compared to other materials such as metal or glass.
The important role of flexible plastic sheets is widely recognized in projects requiring durable and lightweight materials. Many manufacturers have successfully applied flexible plastic sheets to production and achieved significant successes in terms of performance and cost optimization. Some of the areas that can be mentioned are:
- Construction industry: They are designed for moisture barrier and protective shielding applications.
- Food packaging: Flexible plastic sheet are widely used in the production of packaging, food wraps, and other specialized protective films.
- Automotive industry: Common applications of flexible plastic sheet include interior cladding, protective coatings for vehicle parts.
- Product display: They contribute to the production of signs, billboards, cabinets and product display shelves.
- Medical industry: Flexible plastic sheets are popular in the design of trays, medicine containers, medical bags and some equipment covers.
2. Common Types Of Flexible Plastic Sheets
Flexible plastic sheets come in various types, each tailored to meet specific functional and aesthetic needs. Here are some common types of flexible plastic sheet:
2.1. Polyethylene (PE) Sheets
PE sheets are some of the widely used flexible plastic materials, primarily due to their lightweight, durable, and cost-efficient constructions. These polymer sheets resist moisture, chemicals, and impacts, making them very applicable to places where it is very important to shield the effects of external elements.
Primarily, they are used in forms of packaging materials, like plastic wraps, agricultural films, and liners for ponds or landfills.
2.2. Polyvinyl Chloride (PVC) Sheets
PVC sheets are mainly prized for their strength, pliability, and flame-retardant nature. They have both rigid and flexible versions which make them very versatile. Their resistance to chemicals and to wear of UV light enables the feature to exist in a more exposed environment indoors and out.
PVC flexible plastic sheets are usually used within an industrial setting as curtains, weatherproof covers, vinyl flooring, and signage.

2.3. Polycarbonate (PC) Sheets
PC plastic sheets are made of extremely durable materials and have a high optical clarity, which allows a person to use them for many purposes requiring transparency and resistance to impact.
Weighing very light but still incredibly tough, polycarbonate sheets are often placed for safety shields, greenhouse panels, a car windshield, machine guards, and illuminated signage.
2.4. Polypropylene (PP) Sheets
PP sheets are super versatile and have chemical, heat, and wear resistance. Moreover, polypropylene is more valuable in any industry requiring great durability and, more importantly, reusability.
Lightweight and rigid, they are usually used in packaging, stationery folders, medical trays, and automotive components.
Read more: Transforming PP Plastic Sheets with Calcium Carbonate Filler Masterbatch
2.5. Thermoplastic Polyurethane (TPU) Sheets
A TPU flexible plastic sheet has very high elasticity and toughness compared to others. This is because it makes them hard on abrasion, oil, and grease resistance, which makes TPU useful in dynamic environments.
Uses of TPU include automotive interior parts, flexible tubing, medical devices, inflatable products like air mattresses, and other sports equipment.

2.6. Acrylic (PMMA) Sheets
A PMMA flexible plastic sheet is a substitute for glass, which offers lighter and more beautiful alternatives. They remain UV resistant and offer fantastic optical clarity, making them suitable for applications that require a polished and clear finish.
It can also be found in display cases, aquariums, skylights, and decorative panels where aesthetics come first.
2.7. Ethylene Vinyl Acetate (EVA) Sheets
An EVA flexible plastic sheet is soft and lightweight and has superior flexibility and shock absorbing properties. EVA makes the best option for outdoors since they are also waterproof and weather-resistant.
Therefore, they are best used in cushioning materials, yoga mats, footwear components, and sports equipment.

3. Additives To Enhance Flexible Plastic Sheets
Additives are crucial for improving the performance and functionality of a flexible plastic sheet, enabling them to meet the specific demands of various industries. Here are some common additives used in the manufacturing process:
3.1. Filler masterbatch

Filler masterbatch is a compound obtained by mixing virgin polymers with natural minerals such as calcium carbonate (CaCO₃), talc or barium sulfate. Filler masterbatch is added to the production process to replace part of the expensive virgin plastic. This helps to optimize a large amount of production costs for manufacturers. In addition, they enhance optimal properties of the products.
Filler masterbatch increases hardness, thermal stability, and reduces shrinkage during the production process. The flexibility of adjusting parameters makes it easy for manufacturers to design a material that best suits each specific customer’s needs.
For example, adding filler masterbatch to a flexible plastic sheet helps to create a large quantity of food packaging at a low cost while still ensuring perfect protection for the product.
3.2. UV Stabilizers
Prolonged exposure to sunlight can significantly reduce the life and functionality of plastics, especially outdoor plastics. UV stabilizers can be incorporated to protect flexible plastic sheet from the harsh effects of ultraviolet radiation. This helps to prevent the product from fading, becoming brittle, or even breaking down over time.
3.3. Flame retardants
They are one of the important criteria in ensuring safety in both production and daily life. Flame retardants are chemicals added to a flexible plastic sheet to reduce the flammability of the material, slow down the ignition process, and prevent the spread of flames in the event of an accident.
3.4. Antistatic additive

A flexible plastic sheet operating for a long time can cause dust attraction or electrical safety hazards. Antistatic additives eliminate these risks. They prevent static build-up, reduce the attraction of dust and dirt, and provide safety in potentially explosive environments. They are commonly used in electronic equipment applications to help protect the equipment over time.
3.5. Antimicrobials
Flexible plastic sheet requires additives that inhibit the growth of bacteria, fungi and other microorganisms. This process allows for the creation of a protective layer that extends the life of products in harsh conditions.
Antimicrobials protect products from harmful microorganisms, odors and surface degradation over time. Products that emphasize antibacterial properties include food packaging and medical devices. These products will be enhanced for safety to ensure the health of consumers.
3.6. Color masterbatch
Color masterbatch is a concentrated mixture of pigments or dyes that are added to a flexible plastic sheet to achieve the desired colors. They provide the ability to customize aesthetics flexibly while maintaining the properties of the material.
Incorporating this additive into a flexible plastic sheet provides vibrant, long-lasting colors and excellent UV resistance for the product. This is one of the optimal solutions that both meets aesthetic needs and helps attract customers’ attention.
4. Factors to Consider When Choosing Flexible Plastic Sheet For Your Project
Choosing the right flexible plastic sheet is crucial to the success and longevity of your project. Here are some important considerations to help you make the best choice.
4.1. Material properties
A careful determination of the material properties will help flexible plastic sheet to fully demonstrate their strengths in a variety of different applications. Factors such as flexibility, durability, chemical resistance and transparency determine whether the plastic meets the functional requirements of the project.
For this criterion, carefully consider additives that provide additional functionality such as flame retardancy or antistatic properties of the material to help ensure better safety. Consider choosing a flexible plastic sheet with additives such as UV stabilizers or antimicrobials if the material will be exposed to sunlight or microbial environments.
4.2. Application environment
The conditions in which the plastic sheet will operate can greatly affect its performance and longevity over time. Choosing a material that is not compatible with the environment can lead to premature failure or safety hazards.
It is important to consider temperature ranges, humidity, frequency of impact and some environmental impacts. At high temperatures, materials such as PP or PVC may perform better than other materials. If the application is outdoors, consider the effects of UV radiation and choose panels with UV stabilizers to prevent degradation.

5. Conclusion
The success of the project requires the right choice of flexible plastic sheet. Knowledge of the types of flexible plastic materials, additives used in them, and factors affecting performance will help you in choosing a type of material. Keep in mind the material properties and application environment to which the plastic sheet will be subjected, so it always performs optimally. The right choice will make your project more efficient, cost-effective, and long-lasting.
EuP Egypt is proud to be a world leader in high quality plastic material solutions. We commit to provide high quality filler masterbatch, additives and other compounds for the optimal flexible plastic sheet. With 17 years of experience, we are honored to be a trusted partner of plastic manufacturers worldwide. Contact EuP Egypt now to find the optimal plastic material for your project!