Polypropylene sheets, commonly referred to as PP plastic sheets, are versatile materials widely used in various industries. In the manufacturing of PP plastic sheets, the incorporation of filler masterbatch is beneficial. By using filler masterbatch, manufacturers can save production costs and achieve desired characteristics of PP sheets .
1. Understanding PP Plastic Sheets and Filler Masterbatch
What are PP plastic sheets?
PP plastic sheets are thin, flexible sheets made from polypropylene, a thermoplastic polymer. They are widely used due to their excellent chemical resistance, lightweight nature, and ability to be easily molded and shaped. These sheets find applications in packaging, automotive parts, and even in the construction sector.
Read more: What is PP sheet? An Ultimate Guide to Polypropylene Sheet
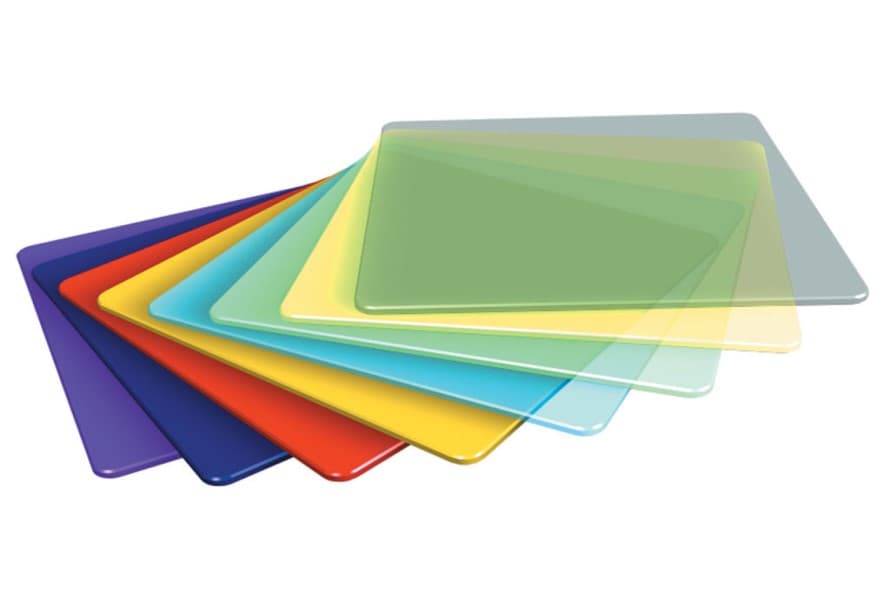
Role of filler masterbatch in PP plastic sheet manufacturing
Filler masterbatch is a concentrated mixture of additives and fillers that are incorporated into the PP plastic sheets during the manufacturing process. Filler masterbatch helps reduce the overall material costs while improving the performance characteristics of the final product.
With the crucial role of filler masterbatch in PP plastic sheet manufacturing, selecting the right type of filler is a key factor determining the final product quality.
2. Types of Filler Masterbatch for PP Sheet Manufacturing
In PP sheet manufacturing, talc and calcium carbonate are the two most commonly used filler masterbatches. Each type possesses distinct characteristics and advantages:
Features | Talc filler masterbatch | Calcium carbonate filler masterbatch |
Main materials | Talc powder, resin, additives | Calcium carbonate powder, resin, additives |
Key advantages |
|
|
Applications | Applications requiring enhanced mechanical properties, high clarity and gloss | Wide range of applications: packaging, construction, automotive components, consumer products |
Additional Notes | Excellent compatibility with polypropylene |
The choice between these two fillers depends on the specific requirements of the end product. However, calcium carbonate has emerged as the preferred choice in PP plastic sheet manufacturing. Let’s explore the key factors driving this preference.
3. Why Choose Calcium Carbonate Filler Masterbatch for PP Plastic Sheet Production?
The selection of calcium carbonate filler masterbatch for PP sheet production stems from its fundamental role in plastic manufacturing. As an abundant natural resource, calcium carbonate provides manufacturers with a cost-effective solution for material optimization, replacing a large amount of virgin resin while maintaining product integrity. This advantage is particularly significant in today’s market, where PP resin prices have shown fluctuations of up to 30% annually.
Calcium carbonate’s exceptional compatibility with PP processing makes it an ideal choice for sheet manufacturing. This advantage, combined with FDA approval for food-contact applications and compliance with international safety standards, makes CaCO3 filler masterbatch an essential component in PP sheet production, serving diverse markets from packaging to automotive applications.

4. Benefits of Using Calcium Carbonate Filler Masterbatch for PP Sheets
The incorporation of calcium carbonate filler masterbatch in PP sheets provides numerous benefits:
Cost Efficiency
Calcium carbonate is generally less expensive than other fillers, which helps in reducing the overall production costs of PP sheets. By replacing up to 60% of virgin PP resin, manufacturers can achieve raw material cost savings of approximately 20%.
Improved Mechanical Properties
Research by Heritage Plastics demonstrates that, with a loading rate of 18%, calcium carbonate significantly improves PP sheets. It boosts heat deflection temperature and impact strength, while maintaining stiffness. Loading levels can be pushed up to 40% without impacting the final product’s integrity.
Improved Processing Efficiency
PP sheets with CaCO3 filler demonstrate faster heating and cooling cycles. This leads to reduced energy consumption and better productivity. Studies also show that this enhanced thermal management lowers shrinkage and warping, ensuring dimensional stability. These processing improvements result in higher output rates and better conversion efficiency in thermoforming.
Environmental Benefits
Environmental studies reveal that using 40% loaded calcium carbonate in PP products can cut greenhouse gas emissions by about 23%. This, along with FDA approval for food contact applications, makes calcium carbonate-filled PP sheets a sustainable option.
Versatility
The use of calcium carbonate allows for a wide range of applications, from packaging materials to construction components.
5. Applications of CaCO3 Filler Masterbatch in PP Sheets

Calcium carbonate filler masterbatch is utilized in various applications of PP sheets, including:
- Packaging: Lightweight, durable, and now more rigid. PP sheets enhanced with calcium carbonate offer superior protection for food and beverages. Calcium carbonate also boosts barrier properties, extending shelf-life while maintaining an attractive appearance.
- Construction: Calcium carbonate-filled PP sheets become robust construction materials, ideal for wall panels, roofing, and insulation. Calcium carbonate’s contribution to weather resistance and structural integrity makes them a smart choice for outdoor applications.
- Automotive: In the automotive sector, PP sheets with calcium carbonate filler are used for interior components, such as door panels, dashboards, and trim. The improved mechanical properties and reduced weight contribute to fuel efficiency and overall vehicle performance. Additionally, the aesthetic advantages of calcium carbonate-filled sheets, such as smooth finishes and customizable colors, enhance the visual appeal of automotive interiors.
- Agricultural Films: Calcium carbonate-filled PP sheets are increasingly being used in agricultural applications, such as greenhouse films and mulching. The sheets provide excellent durability against UV radiation and environmental stressors while offering cost-effective solutions for farmers.
- Consumer Products: The versatility of calcium carbonate filler makes it suitable for various consumer products, including storage containers, furniture components, and educational materials. The combination of durability and reduced weight enhances usability and convenience for end-users.
6. PP Sheet Manufacturing Process Involving Calcium Carbonate Filler Masterbatch
The manufacturing process of PP sheets incorporating calcium carbonate filler masterbatch typically involves several key steps:
- Material Preparation: Polypropylene resin is mixed with calcium carbonate filler masterbatch in a controlled ratio to achieve the desired properties. This initial blending ensures that the filler is evenly distributed within the polymer matrix, which is critical for the performance of the final product.
- Extrusion: The mixture is then fed into an extruder, where it is melted and formed into sheets. The extrusion process involves heating the material to a specific temperature, allowing it to flow and be shaped into sheets. The design of the extruder and the temperature settings are optimized to ensure uniform distribution of calcium carbonate throughout the PP matrix, which results in consistent mechanical properties across the sheets.
- Cooling and Cutting: Newly extruded sheets are rapidly cooled to solidify the polymer and retain the desired thickness. Then the sheets are cut to the required dimensions. This step is carefully managed to avoid any warping or dimensional errors.
- Quality Control: All finished sheets undergo stringent quality checks, including mechanical property testing and visual inspections. Advanced techniques analyze the calcium carbonate dispersion. This ensures the final product meets industry standards.
- Packaging and Distribution: Properly packaged sheets are then prepared for distribution. This protective packaging ensures products are delivered in pristine condition.

7. EuP Egypt – The World Leading Calcium Carbonate Filler Masterbatch Supplier

EuP Egypt is a prominent manufacturer in the filler masterbatch sector and a key member of the EuP Group, the world leader in masterbatch solutions. With 17 years of extensive experience and a modern facility, we have positioned ourselves as a trusted partner for plastic manufacturers throughout the African region.
Our PP filler masterbatch, specifically the EFPP, is meticulously designed to meet the rigorous demands of PP sheet manufacturing. This innovative product combines high-quality CaCO3 powder, PP resin, and advanced additives, ensuring exceptional performance in sheet production.
The EFPP formulation is specifically tailored to:
- Facilitate cost-effective production by replacing up to 50% of virgin PP resin.
- Enhance the mechanical properties.
- Improve processing efficiency through optimized thermal characteristics.
- Guarantee consistent product quality and dimensional stability.
Contact us now for more details of PP filler masterbatch for PP plastic sheets manufacturing!
8. Conclusion
In conclusion, PP plastic sheets are an essential material in various industries, and the use of calcium carbonate filler masterbatch significantly enhances their performance and cost-effectiveness. With benefits such as improved mechanical properties, better surface finish, and environmental advantages, calcium carbonate is a preferred choice for manufacturers looking to optimize their PP sheet production.