Fiberglass is a type of FRP (fiber-reinforced polymer) using glass fibers, offering affordability and versatility for general applications like construction and marine projects. FRP encompasses a broader range of fibers (e.g., carbon, aramid) for specialized, high-performance needs. Choose based on budget, strength, and environmental conditions.
Confused about whether FRP or fiberglass is the right material for your project? This guide clarifies the differences and similarities between Fiber-Reinforced Plastic (FRP) vs fiberglass, two composite materials widely used in construction, marine, automotive, and energy industries. Written by materials experts, this article draws on industry standards and practical insights to help you make informed decisions.
1. What is Fiberglass? Understanding the Basics
Fiberglass is a type of reinforced material made by weaving or matting glass fibers together and combining them with a plastic resin. The result? A strong, lightweight material that’s surprisingly versatile.
To make fiberglass, manufacturers start by melting raw glass. That molten glass is then pulled into fine threads. These threads, or filaments, are bundled together into yarns, woven into mats, or chopped into small pieces, depending on how they’ll be used. Finally, they’re combined with a resin—usually polyester or epoxy—to form a durable composite.
One thing to keep in mind: fiberglass is not a standalone material. It needs a resin to hold the glass fibers together. This combination of glass and polymer is what gives fiberglass its unique performance.
You might also hear it called glass fiber-reinforced plastic (GFRP) or simply glass fiber composite. No matter the name, fiberglass is one of the most common and cost-effective composite materials on the market today.
👉 Want to dive deeper into how fiberglass works? Check out our full article on glass fiber-reinforced plastic
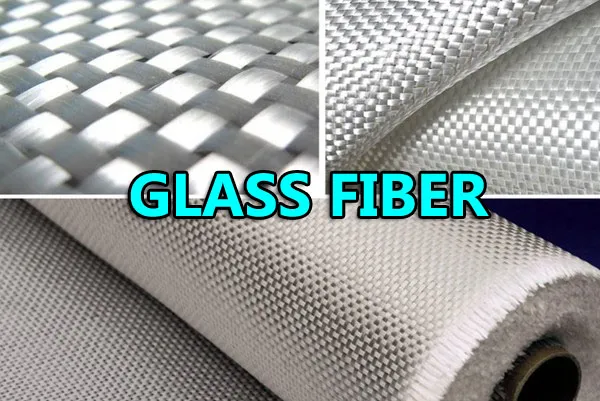
2. What is FRP? Exploring Fiber-Reinforced Polymers
FRP, or fiber-reinforced polymer, is a composite material made by combining strong fibers with a plastic matrix. Think of it as a team effort: the fibers provide the strength, while the polymer binds everything together and helps the material hold its shape.
What makes FRP special is its flexibility in design. Manufacturers can choose from different types of fibers depending on the needs of the project. These include:
- Glass fibers (which make fiberglass),
- Carbon fibers (for extra strength and stiffness),
- Aramid fibers (like Kevlar, known for impact resistance),
- Basalt or natural fibers in some eco-friendly variants.
The polymers used as the “glue” are typically thermoset resins or thermoplastic resins:
- Thermoset Resins: Epoxy, vinyl ester, or polyester, which harden permanently.
- Thermoplastic Resins: Emerging for recyclability (e.g., polypropylene).
FRP can be molded into complex shapes, designed to resist harsh environments, or tailored for high strength-to-weight performance.
You’ll also come across terms like GFRP (glass fiber-reinforced polymer) or CFRP (carbon fiber-reinforced polymer)—these just specify the type of fiber used in the mix.
👉 Curious to learn more about the different types of FRP? Explore our full guide on fiber-reinforced polymers (FRP plastic)

3. Key Differences Between FRP and Fiberglass
You might be wondering: If fiberglass is a type of FRP, then what exactly sets them apart? Good question. Let’s break it down.
1. Composition
This is the biggest difference.
- FRP is a category. It includes any composite made of a fiber (glass, carbon, aramid) and a polymer resin.
- Fiberglass is just one type of FRP—specifically made with glass fibers.
So, all fiberglass is FRP, but not all FRP is fiberglass.
2. Strength and Performance
- FRP can be engineered to meet specific strength, stiffness, or flexibility needs, depending on the fiber used. For example, carbon fiber-reinforced FRP is much stronger and lighter than fiberglass.
- Fiberglass offers good performance at a low cost, but it doesn’t match the high-end specs of carbon or aramid-based FRP.
3. Weight and Density
- Fiberglass is relatively lightweight, which is why it’s used in boats, cars, and aircraft.
- Other FRPs (like CFRP) can be even lighter while offering more strength—but at a higher cost.
4. Corrosion Resistance
- Both materials resist corrosion well.
- However, resistance levels depend more on the type of resin used (epoxy vs polyester) than the fiber itself.
5. Cost
- Fiberglass is generally more affordable and easier to produce.
- Custom FRPs with advanced fibers or high-performance resins can get expensive fast.
📊 Quick Comparison Table: FRP vs Fiberglass
Property | FRP (General) | Fiberglass (GFRP) |
Composition | Fiber + polymer (any type) | Glass fiber + polymer |
Strength | Varies (high with carbon or aramid) | Moderate (500–700 MPa) |
Weight | Lightweight to ultra-light | Lightweight |
Corrosion Resistance | Excellent (resin-dependent) | Excellent |
Cost | Varies (higher for carbon/aramid) | Low to moderate (~$2–$5/kg) |
Flexibility | High—customizable | Good, but limited to glass fiber |
4. Similarities Between FRP and Fiberglass
Now that we’ve covered how FRP and fiberglass differ, let’s look at what they have in common—because there’s plenty of overlap.
1. Lightweight yet Strong
Both FRP and fiberglass are known for having a high strength-to-weight ratio. That means they offer impressive durability without adding a lot of weight. This is why both are popular in aerospace, automotive, and marine industries.
2. Corrosion Resistance
Whether it’s fiberglass or another type of FRP, these materials are built to resist corrosion. They perform well in tough environments—think saltwater, chemicals, or industrial gases—especially when paired with the right resin. (per ISO 12944)
3. Non-Conductive Properties
Another shared trait? Both materials are non-conductive, making them ideal for electrical applications or environments where insulation is key.
4. Versatile Applications
FRP and fiberglass are used in many of the same industries—construction, transportation, energy, and infrastructure. While the fiber type might differ, the roles they play are often similar.
5. Interchangeable in Casual Use
In everyday conversation, people often say “FRP” when they mean “fiberglass” and vice versa. While it’s technically not accurate, the terms do get used interchangeably, especially when the FRP in question is glass-based (GFRP).
In short, fiberglass may be a subset of FRP, but it shares many of the same benefits and applications. If you’re using one, chances are you’re already working within the broader FRP family.
5. Applications of FRP and Fiberglass in Industry
Both FRP and fiberglass have carved out essential roles across many industries—thanks to their durability, strength, and resistance to harsh conditions. But while they often overlap, there are also some unique applications for each.
Common Uses of Fiberglass
Fiberglass is a go-to material when you need something that’s strong, lightweight, and affordable. It’s widely used in:
- Construction: roofing panels, insulation, wall reinforcements
- Automotive: body kits, hoods, bumpers, RV panels
- Marine: boat hulls, decks, and storage tanks
- Consumer products: ladders, tool handles, surfboards
It’s also popular in electrical insulation, thanks to its non-conductive nature.
Common Uses of FRP plastic
FRP’s strength lies in its versatility. Because it’s a broader category, it can be engineered with different fiber types to suit more demanding environments. You’ll find FRP in:
- Infrastructure: pedestrian bridges, structural beams, rebar
- Industrial: chemical tanks, corrosion-resistant grating, cable trays
- Transportation: lightweight aircraft parts, train interiors
- Energy: wind turbine blades, solar panel frames, oil and gas equipment
One niche example? FRP cable trays are preferred in power plants and industrial facilities because they’re corrosion-resistant, easy to install, and don’t conduct electricity.
Choosing Based on Application
- Use fiberglass for general-purpose needs where cost and ease of use matter.
- Opt for custom FRP solutions when you need higher strength, special fiber types, or resistance to extreme heat, chemicals, or loads.
6. Advantages and Disadvantages of FRP vs Fiberglass
When choosing between FRP and fiberglass, it’s important to weigh the pros and cons of each. While they share a lot of qualities, they perform differently depending on the situation—and your budget.
Fiberglass: Pros and Cons
Advantages:
- Cost-Effective: Fiberglass is one of the most affordable composite materials available.
- Widely Available: It’s used so commonly that sourcing and manufacturing are simple.
- Good Strength: It offers solid mechanical properties for most general applications.
- Corrosion-Resistant: With the right resin, fiberglass holds up well against moisture, salt, and chemicals.
Disadvantages:
- Limited Performance: Compared to carbon or aramid fibers, fiberglass isn’t as strong or stiff.
- Less Tailored: You get what’s available—there’s less room for customization in structure or performance.
- Can Be Brittle: Under high stress or repeated flexing, it may crack over time.
FRP (General): Pros and Cons
Advantages:
- Highly Customizable: You can choose the fiber (glass, carbon, aramid) and resin to match exact needs.
- Stronger Options Available: Carbon or aramid-reinforced FRPs can outperform fiberglass by a long shot.
- High Strength-to-Weight Ratio: Ideal for aerospace, performance vehicles, and structural parts.
- Superior Durability: Great for long-term exposure to harsh environments.
Disadvantages:
- Higher Cost: Advanced FRPs can be expensive to produce.
- More Complex to Manufacture: Custom molds, fiber layout, and resin selection take time and expertise.
- Repair & Recycling Can Be Tricky: Especially for thermoset-based FRPs.
In short, fiberglass is great when you need something affordable and reliable. But if your project calls for specialized performance or extreme durability, a custom FRP might be worth the investment.
7. Which Material Should You Choose for Your Project?
So—FRP or fiberglass? The best choice depends on what you’re building and what you need the material to do. Let’s break it down.
Start with Your Priorities
- If you’re looking for something affordable, easy to work with, and widely available, fiberglass is a solid choice.
- If your project demands higher strength, advanced performance, or long-term durability in harsh conditions, a customized FRP might be the better fit.
Think About the Environment
- Wet, salty, or chemical-heavy setting? Both materials resist corrosion, but you might want an FRP engineered specifically for that environment.
- Electrical safety concerns? Fiberglass and FRP are both non-conductive, but make sure the resin system also meets your needs.
Consider Budget and Scale
- For cost-sensitive jobs like automotive body kits, building insulation, or storage tanks, fiberglass is the go-to.
- For high-performance applications—like structural reinforcements, bridges, or aerospace parts—carbon or aramid-based FRPs are worth the extra investment.
Ask These Quick Questions:
- Do I need extreme strength or just good enough?
- Will the part be exposed to weather, chemicals, or heavy wear?
- Is budget the top priority? Or performance?
Use fiberglass when you want functionality at a lower cost. Choose FRP when you need a tailored, high-performance solution.
8. FRP vs Fiberglass in Sustainability and Innovation
In today’s world, it’s not just about performance—it’s also about how materials impact the environment. So how do FRP and fiberglass measure up in terms of sustainability and innovation?
Sustainability Concerns
Both fiberglass and FRP are durable, long-lasting materials, which reduces the need for frequent replacements. That’s a plus for sustainability.
But on the flip side, traditional composites—especially thermoset-based FRPs—can be difficult to recycle. Once cured, these materials don’t melt or reshape like some plastics do. This has raised concerns about their end-of-life impact.
Still, progress is being made. Some companies are developing recyclable thermoplastic resins and greener fiber options, like natural or basalt fibers, to reduce environmental footprints.

Innovations in Composite Technology
Modern manufacturing techniques like pultrusion and resin transfer molding (RTM) are making FRP production more energy-efficient and precise. There’s also a rise in bio-based resins—renewable alternatives to traditional petrochemical resins.
In the fiberglass world, lighter and more efficient weaves are being designed to maintain strength while reducing material use. These innovations improve both performance and sustainability.
While both materials still face challenges in recycling, the industry is evolving. If sustainability is a key priority for your project, ask your supplier about eco-friendly composites or recyclable FRP options.
Tip: Ask suppliers for ISO 14001-certified materials or natural fiber options for greener projects.
9. Conclusion
Understanding the difference between FRP and fiberglass comes down to one key point: fiberglass is a type of FRP, but not all FRP is fiberglass. While both materials offer strength, light weight, and resistance to corrosion, the right choice for your project depends on your specific needs—whether it’s performance, cost, or environmental conditions.
At EuP Egypt, we’re proud to contribute to this field as a reliable supplier of glass fiber-reinforced engineering compounds. As part of the EuP Group—a leader in the masterbatch industry since 2008—we’ve supported over 500 industrial projects across sectors like automotive and construction. Our materials meet ISO 9001 and ISO 14001 standards, ensuring both quality and environmental responsibility.
While this guide is based on industry-standard information, feel free to reach out if you’re seeking expert advice for your application.
📩 Contact us at info@eupegypt.com or visit our Contact us to learn more.
10. FAQ: FRP vs Fiberglass
1. What is the difference between FRP and fiberglass?
FRP (fiber-reinforced polymer) is a broad category of composite materials made from fibers and a polymer matrix. Fiberglass is a specific type of FRP that uses glass fibers as reinforcement. So, all fiberglass is FRP, but not all FRP is fiberglass.
2. Can FRP and fiberglass be used interchangeably?
Yes, for general applications like marine or construction, but advanced FRPs (e.g., CFRP) are needed for high-performance uses.
3. What are the main applications of FRP composites?
FRP is used in a wide range of industries—construction, automotive, marine, and energy. You’ll find it in things like cable trays, structural beams, tanks, and bridges. Fiberglass, as a form of FRP, is common in insulation, boat hulls, and car parts.
4. Is fiberglass cheaper than FRP?
Yes, fiberglass costs $2–$5/kg, while advanced FRPs (like carbon or aramid fibers) can reach $50/kg.
5. How do FRP and fiberglass compare in corrosion resistance?
Both materials offer excellent corrosion resistance, especially when paired with the right resin (like epoxy or vinyl ester). That’s why they’re often used in marine and chemical environments.
6. Which is better for marine applications?
Fiberglass is cost-effective for boat hulls; CFRP is better for lightweight, high-performance vessels.
7. How do FRP and fiberglass impact the environment?
Both are durable but hard to recycle. Emerging thermoplastic FRPs and bio-based resins improve sustainability.