Thermosetting plastics are a key component in various industries due to their unique properties. Once molded and cured, they cannot be reshaped, making them ideal for demanding applications like electrical components, automotive parts, and construction materials. In this article, we will explore everything about thermosetting plastics and a detailed selection guide for your projects.
1. What is Thermosetting Plastic?
Thermosetting plastic or thermosetting resin is a polymer irreversibly hardened by heat. The starting material for a thermoset is a liquid or soft solid. Heat provides energy for covalent bond formation, cross-linking the polymer subunits and curing/hardening the plastic. Sometimes the heat is applied externally, but it may come from the chemical reaction of mixing ingredients. Adding pressure, a catalyst, or a hardener can increase the curing rate. Once cured, a thermosetting plastic cannot be remelted, so it is formed into its final shape by injection molding, extrusion molding, compression molding, or spin casting.

2. Properties of Thermosetting Plastics
Thermosetting plastics possess several properties that contribute to their widespread use in various industries. Some of the key properties of thermosetting plastics are:
2.1. High Thermal Stability
Thermosetting plastics exhibit excellent heat resistance and can withstand high temperatures without softening or deforming. This property makes them suitable for applications where exposure to elevated temperatures is involved, such as automotive engine components and electrical insulators.
2.2. Chemical Resistance
Thermosetting plastics have high resistance to a wide range of chemicals, including acids, bases, solvents, and oils. They are less prone to degradation or corrosion when exposed to harsh chemical environments, making them suitable for chemical processing equipment, storage tanks, and chemical-resistant coatings.
2.3. Dimensional Stability
Once cured, thermosetting plastics maintain their shape and dimensional stability even under changing environmental conditions. They have low coefficients of thermal expansion, meaning they do not expand or contract significantly with temperature fluctuations. This property ensures precise and consistent part dimensions over a wide range of temperatures.
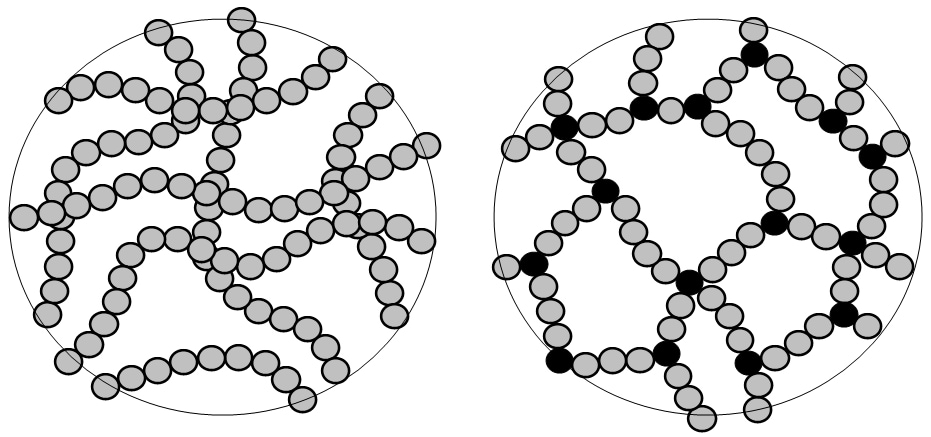
2.4. Mechanical Strength
Thermosetting plastics exhibit excellent mechanical strength and stiffness, providing structural integrity to components. They have high tensile, compressive, and flexural strength, making them suitable for load-bearing applications. Reinforcing materials, such as fiberglass or carbon fibers, can further enhance their mechanical properties.
2.5. Electrical Insulation
Many thermosetting plastics possess excellent electrical insulating properties, making them valuable in electrical and electronics applications. They have low electrical conductivity, high dielectric strength, and are resistant to electrical arcing. These properties make them suitable for electrical enclosures, circuit boards, and insulating coatings.
2.6. Flame Resistance
Thermosetting plastics often exhibit good flame resistance due to their inherent chemical structure and cross-linking. They have high ignition temperatures and low flammability, making them suitable for applications that require fire-resistant materials, such as electrical connectors, switches, and fire safety equipment.
2.7. Impact Resistance
Some thermosetting plastics have good impact resistance, allowing them to withstand sudden impacts and shocks without fracturing. This property is important in applications where durability and resistance to mechanical impact are critical, such as automotive bumpers and sports equipment.
3. Thermosetting Plastic Examples
Here are some common examples of thermosetting plastics and their uses:
- Epoxy Resins: Commonly used in adhesives, coatings, and composite materials. Strong, durable, and resistant to heat and chemicals.
- Phenolic Resins: Used in circuit boards and electrical insulators. High heat resistance and excellent electrical insulation properties.
- Urea-Formaldehyde: Widely used in particleboard, plywood, and molding applications. Rigid, strong, and heat-resistant.
- Melamine: Found in kitchenware, laminates, and coatings. Known for being hard, durable, and resistant to scratching.
- Polyurethane: Used in foam, insulation, and coatings. Flexible or rigid, depending on the formulation.
- Polyester: Commonly used in fiberglass reinforcements and coatings. Offers excellent chemical resistance, durability, and stability in harsh environments.
- Silicone: Found in sealants, adhesives, and medical implants. Heat-resistant, flexible, and retains its properties over a wide range of temperatures.

4. Applications
Thermosetting plastics find a wide range of applications across various industries due to their exceptional properties. Some of the main applications of thermosetting plastics include:
4.1. Automotive Industry
Thermosetting plastics are used in the automotive industry for various components, such as engine parts, electrical connectors, braking systems, interior trim, and exterior body panels. Their high heat resistance, dimensional stability, and mechanical strength make them ideal for withstanding the demanding conditions in automotive environments.
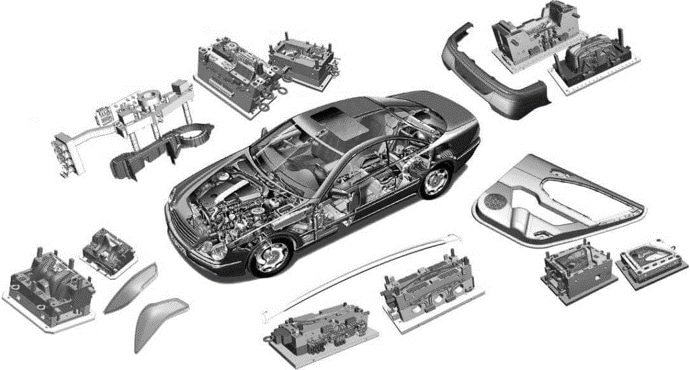
4.2. Electronics Industry
Thermosetting plastics are extensively used in electrical and electronics applications due to their excellent electrical insulation properties. They are employed in the production of circuit boards, electrical enclosures, insulating coatings, connectors, and switches. Their resistance to heat and chemicals ensures the safe and reliable functioning of electrical equipment
4.3. Aerospace Industry
The aerospace industry relies on thermosetting plastics for lightweight yet strong components. These plastics are used in aircraft interiors, structural elements, radomes, and electrical insulation systems. Their high strength-to-weight ratio, flame resistance, and dimensional stability are crucial for meeting stringent safety and performance requirements.
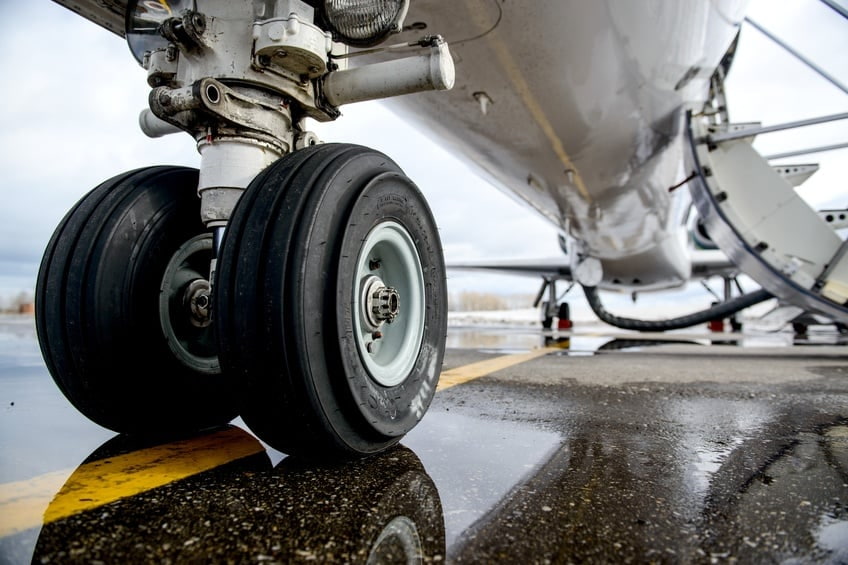
4.4. Construction Industry
Thermosetting plastics are utilized in the construction sector for a variety of applications. They are used in insulation materials, decorative laminates, adhesives, coatings, and composite panels. The excellent fire resistance, chemical resistance, and durability of thermosetting plastics make them suitable for applications requiring long-term performance in harsh environmental conditions.
4.5. Consumer Goods
Thermosetting plastics are found in a range of consumer goods, including kitchen appliances, furniture, sporting equipment, and household fixtures. They provide durability, impact resistance, and aesthetic appeal in products such as countertops, handles, casings, and laminates.
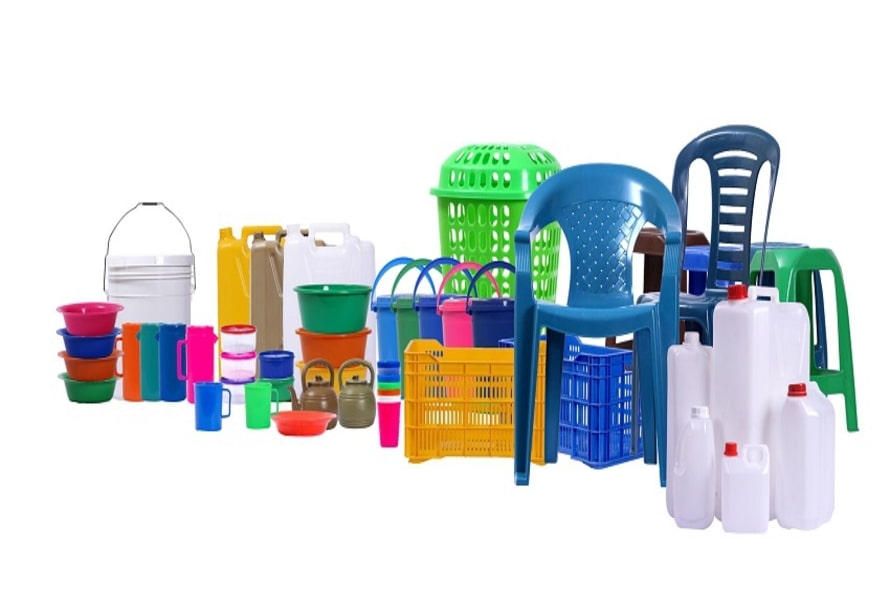
4.6. Industrial Equipment
Thermosetting plastics are used in industrial equipment and machinery due to their high resistance to heat, chemicals, and wear. They are employed in pumps, valves, gaskets, seals, bearings, and tooling components. The dimensional stability and mechanical strength of thermosetting plastics ensure reliability and extended service life in industrial settings.
4.7. Medical and Healthcare
Thermosetting plastics play a role in medical and healthcare applications, including medical device components, surgical instruments, dental products, and laboratory equipment. Their biocompatibility, chemical resistance, and sterilizability make them suitable for use in critical healthcare environments.

5. Advantages and Disadvantages of Thermosetting Plastic
5.1. Advantages
The benefits that thermosetting plastic can offer over its metal counterparts include:
- Choice of color and surface finishes
- Resistance to corrosion effects and water
- Available molded-in tolerances
- High mechanical property
- Low thermal conductivity and microwave transparency
- High strength-to-weight ratio and performance
- Outstanding dielectric strength
- Lower tooling/set-up costs
- Cost-effective
- Excellent dimensional stability
- Reduced production costs over fabrication using metals
5.2. Disadvantages
There are certain disadvantages to the use of thermosetting plastic:
- It cannot be recycled.
- low tensile strength and ductility
- It cannot be remolded or reshaped.
- Poor thermal conductivity for housing replacements.
- Much more difficult to surface finish.
- The rigidity of the material can result in product failure when used in high-vibration applications.
6. Selection Criteria
Choosing the right thermosetting plastic depends on several factors:
- Application Requirements: Identify the specific properties you need, such as heat resistance, strength, or electrical insulation.
- Chemical Compatibility: Ensure the plastic can withstand exposure to chemicals in your application.
- Cost: Evaluate the cost of production and suitability for your budget.
- Environmental Factors: Consider temperature, humidity, and other environmental conditions.
- Safety Standards: Ensure the material meets industry safety and regulatory standards.
7. FAQs
7.1. How do thermosetting plastics compare to thermoplastics?
The main distinction between the two is that thermoset is a material that strengthens when heated but cannot be remoulded or heated after initial forming, whereas thermoplastics can be reheated, remoulded, and cooled as needed without causing any chemical changes.
Read more: Key differences between thermoplastic and thermosetting plastic
7.2. What is the curing process for thermosetting plastics?
The curing process for thermosetting plastics is responsible for their polymerization and the formation of the molecular crosslink network of bonds that give thermosets their desirable mechanical properties. This process solidifies the polymer matrix, thereby locking the composite part into its desired shape. Completion of the curing process (complete chemical reaction) is critical for obtaining the full mechanical properties of the polymer.
7.3. Can thermosetting plastics be recycled?
The particular features of thermosetting plastics make all objects made with this type of polymers particularly difficult to recycle, because the bonds that are created during the plastic solidification and relevant cross-links are final and cannot be dissolved.
8. Conclusion
In conclusion, thermosetting plastics offer a range of valuable properties and applications in various industries. Their ability to undergo irreversible chemical changes during curing, resulting in a rigid and heat-resistant structure, makes them ideal for high-temperature environments. The dimensional stability, strength, and resistance to chemicals make them indispensable in fields such as automotive, aerospace, and electrical insulation. The continued advancements in thermosetting plastic technology will undoubtedly pave the way for further innovations and applications in the future.
EuP Egypt, a proud member of the EuP Group, is a global leader in filler masterbatch production with over 17 years of expertise. Our company offers high-quality products, including bioplastic compounds, color masterbatch, additives, engineering plastic compounds, filler masterbatch and bio filler. With cutting-edge technologies and extensive expertise, these products are designed to enhance both the functionality and aesthetics of plastic products across various industries. Using advanced technology and expertise, EuP Egypt ensures that its products consistently meet top industry standards. Contact us now!