Jumbo bags, essential for transporting and storing bulk materials, are meticulously crafted using advanced techniques and durable materials. Their production ensures reliability and efficiency across industries. Understanding the manufacturing process is key to appreciating their quality and functionality. This article will provide a comprehensive overview of how jumbo bags are made, focusing on their materials, production methods, and key applications.

1. Jumbo Bags Overview
1.1. What is a Jumbo Bag?
A jumbo bag, also known as a Flexible Intermediate Bulk Container (FIBC), is a large, flexible container designed for storing and transporting dry, flowable products such as sand, fertilizer, and granules of plastic. Typically made from woven polypropylene, these bags are capable of holding between 500 kg and 2,000 kg of material.
1.2. Common Uses
Jumbo bags are widely utilized across various industries due to their versatility and capacity. Common applications include:
- Agriculture: Transporting grains, seeds, fertilizers, and other agricultural products.
- Construction: Handling materials like sand, cement, and gravel.
- Chemical Industry: Storing and transporting chemicals and powdered metals.
- Mining: Carrying minerals and ores.
- Food Industry: Packaging ingredients such as sugar, flour, and rice.
Their robust design ensures safe handling and storage of bulk materials.
1.3 Types of Jumbo Bags
Jumbo bags come in various types, each suited to specific applications. let’s explore their classifications based on different structures:
Mouth Type
Jumbo bags can be categorized by their openings:
- Hooded Jumbo Bag: These bags feature an expandable mouth, ideal for bulk goods, large lumps, or low-dust powders such as corn silage and animal feed ingredients.
- Tube Cap Jumbo Bag: Designed with a round tube at the top (also called a loading tube), this bag is commonly used for powdered goods such as plastic granules, chemicals, rice, and cement. The tube may be zippered or funnel-style, with a tie to close the bag.
- Open Lid Jumbo Bag: These bags have a fully open top, suitable for block-shaped goods like pressed sawdust, waste, and small bags weighing 25-50 kg.
Bottom Type
Jumbo bags can also be classified based on their bottom design:
- Flat Bottom Jumbo Bag: Typically used for products that do not need bottom discharge, these are often for block-shaped items.
- Discharge Bottom Jumbo Bag: Featuring a round tube (exhaust pipe) with a string for easy product release, these bags are ideal for automatic packing and discharging, especially for fine powders to prevent spillage.
Shape
The shape of the jumbo bag determines its usage:
- Square Jumbo Bag: Ideal for agricultural products (rice, coffee, animal feed), food items (sugar, milk powder), and industrial goods (chemicals, plastic, construction materials).
- Round Jumbo Bag: With a cylindrical shape, this bag is perfect for fine powders like oxide, minerals, and chemicals, often featuring a bottom belt system for easier transport.
Electrostatic properties
- Type A: Made from standard polypropylene, these bags offer no static protection and are suitable for non-flammable materials.
- Type B: Constructed from materials with a low breakdown voltage, these bags are resistant to propagating brush discharges and are used for non-flammable products.
- Type C: Made from conductive materials, these bags are designed to control electrostatic charges by grounding and are suitable for environments where flammable or combustible materials are present.
- Type D: Anti-static FIBCs that dissipate static charges without the need for grounding, suitable for transporting flammable materials.
Strap Type
Jumbo bags also differ in their lifting straps:
- 2 Lifting Straps: These bags are equipped with two straps for crane lifting, enabling multiple bags to be hoisted simultaneously.
- 4 Lifting Straps: Four evenly spaced straps are sewn in a U-shape, providing strong load-bearing capacity, and making the bags suitable for forklift and crane handling.
- Sling Bag: These bags have a PP woven bottom fabric with securely sewn lifting belts and four additional walls. They are designed for heavy block goods or bags like cement, rice, or plastic beads, with a load capacity of 40-50 kg.
2. Jumbo Bag Materials: What Are FIBC Bags Made Of?
Jumbo bags (FIBCs), are primarily made from woven polypropylene (PP) fabric. This material is chosen for its strength, durability, and flexibility, making it suitable for storing and transporting various dry, flowable products such as sand, fertilizer, and plastic granules.
To enhance the properties of PP used in jumbo bags, manufacturers often incorporate filler masterbatch. Filler masterbatch is a concentrated mixture of additives and fillers, such as calcium carbonate (CaCO₃), blended into the polymer during the extrusion process. The primary purposes of using filler masterbatch include:
- Cost Reduction: Incorporating fillers like CaCO₃ reduces the amount of pure PP required, thereby lowering material costs.
- Improved Physical Properties: Fillers can enhance the stiffness, tensile strength, and dimensional stability of the final product.
- Enhanced Processability: The addition of fillers can improve the processing characteristics of the polymer, facilitating easier manufacturing of the bags.
It’s important to note that the specific formulation of filler masterbatch can vary based on the desired properties of the jumbo bags and the nature of the products they are intended to carry. Manufacturers may customize the filler masterbatch to meet specific performance requirements, such as UV resistance, antistatic properties, or color.
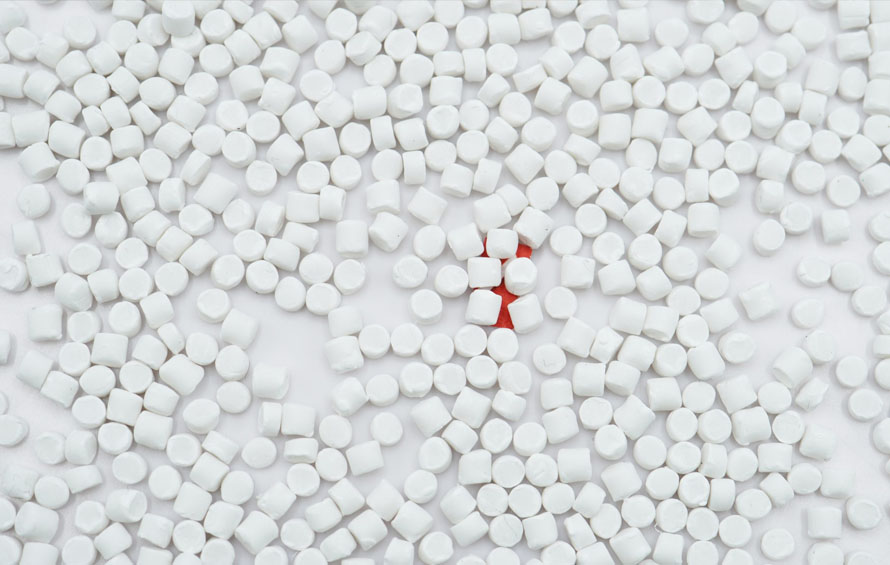
3. Jumbo Bags Manufacturing Process
The jumbo bags manufacturing process involves several key steps to ensure the bags meet the required strength, durability, and functionality.
Step 1 – Extrusion
Polypropylene (PP) resin is melted and formed into tapes of specific thicknesses and widths. This stage ensures the tapes possess the necessary tensile strength for the bags.

Step 2 – Weaving
The PP tapes are wound onto bobbins and woven into fabric using specialized looms. This fabric forms the body of the jumbo bag and is designed to be strong enough to carry goods while allowing for breathability.
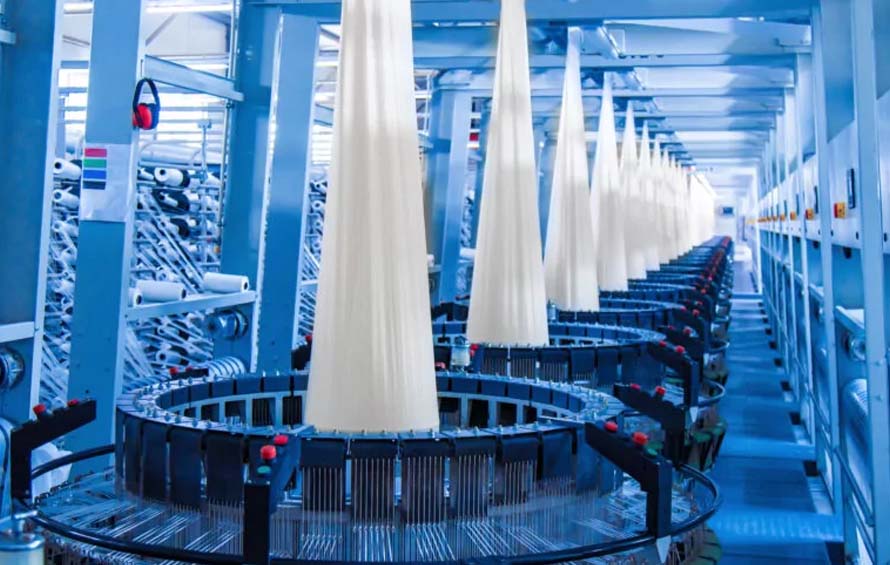
Step 3 – Moisture Proofing (Optional)
Depending on requirements, a special coating is applied to the fabric to make it moisture-resistant. This is particularly important for storing and transporting products sensitive to moisture.
Step 4 – Cutting
The woven fabric is cut into specific shapes and sizes based on the bag’s design. Precision cutting ensures uniformity and accuracy in the bag’s dimensions.
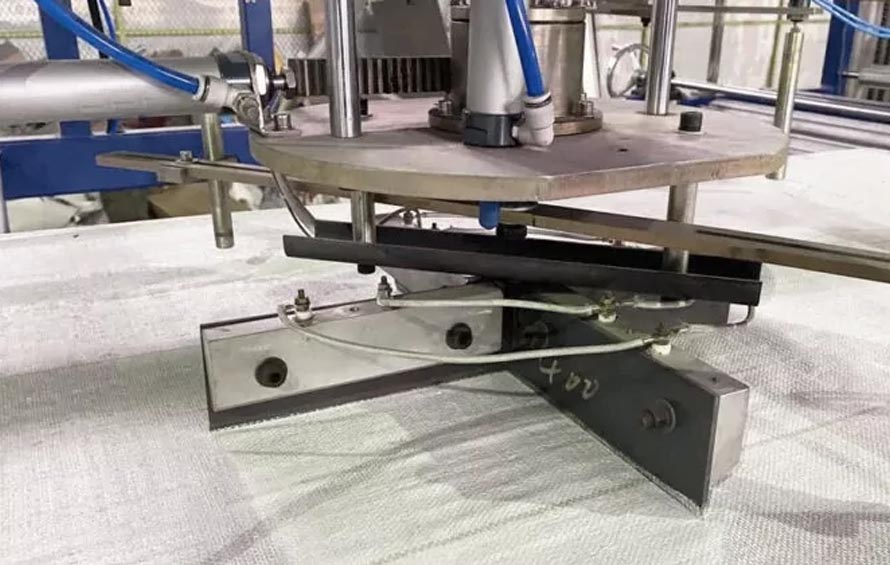
Step 5 – Printing
The cut fabric pieces are printed with necessary information, such as company logos or handling instructions, using FDA-approved inks suitable for food contact.

Step 6 – Webbing
Strips of PP fabric are woven to create the handles or lifting loops of the bag. These handles are essential for the safe handling and transportation of the filled bags.
Step 7 – Sewing
The various components, including the body fabric and webbing, are sewn together to form the final jumbo bag. This step requires skilled labor to ensure the bags are constructed to withstand the intended loads.
Step 8 – Final Testing
The completed bags undergo rigorous testing to ensure they meet safety and quality standards. This may include load testing to verify the bag’s capacity and durability.
Understanding this manufacturing process is crucial for selecting the appropriate jumbo bag for specific applications, ensuring both safety and efficiency in material handling.
4. Design Features and Specifications
Jumbo bags are designed with specific features and specifications to ensure safe and efficient handling of bulk materials. Key design features and specifications include:
Material and Construction
- Fabric: Typically made from woven polypropylene (PP) fabric, which offers strength and durability.
- Coating: Some bags are coated to provide moisture resistance, while uncoated versions are breathable.
Design Types
- Circular Bags: Constructed as a single, circular, woven tubular fabric without side seams, reducing weak points.
- U-Panel Bags: Made from a single piece of fabric forming a U-shape, providing better shape retention.
- Four-Panel Bags: Comprising four pieces of fabric sewn together, offering enhanced shape stability.
- Baffle Bags: Incorporate internal baffles to maintain a square shape and improve stackability.
Dimensions and Capacity
- Standard Sizes: Common base dimensions are 35″ x 35″, with heights ranging up to 96″.
- Capacity: Typically designed to hold up to 1,000 kg, though larger units can store more.
Lifting and Handling
- Lift Loops: Equipped with one, two, or four lifting loops for easy handling.
- Discharge Options: May include spouts at the top or bottom for efficient filling and emptying.
Safety and Compliance
- Safety Factor: Standard safety factor is 5:1, indicating the bag can safely carry five times its rated load.
- Certifications: Some bags are UN certified for transporting hazardous materials.
Additional Features
- Linings: Optional internal liners made from polyethylene or other materials to protect contents from moisture or contamination.
- Ventilation: Ventilated designs allow airflow, suitable for perishable goods.
- Printing: Custom printing for branding and handling instructions.

5. Conclusion
In conclusion, the process of making jumbo bags is a meticulous journey that involves the selection of high-quality polypropylene, precise weaving, and careful stitching to create a strong, durable product capable of handling heavy loads. From extrusion to final testing, each step ensures that the bags meet stringent standards for safety and efficiency.
With advancements in technology and material science, EuP Egypt have enhanced their offerings by providing high-quality filler masterbatch products, especially PP filler masterbatch for PP jumbo bags, which improve the strength and durability of materials used in manufacturing jumbo bags. EuP Egypt’s filler masterbatch solutions provide added value, ensuring that the bags are robust and meet specific industry requirements.
If you’re looking to explore high-quality jumbo bags for your business, or need expert advice on materials like filler masterbatch, contact us today for tailored solutions.