The Melt Flow Index (MFI) measures how easily a polymer flows when melted, guiding material selection for processes like injection molding or extrusion. Use our detailed MFI table to compare common polymers and choose the right material for your manufacturing needs.
1. What is the Melt Flow Index (MFI) of Polymers?
The Melt Flow Index (MFI)—also known as Melt Index (MI) or Melt Flow Rate (MFR), measures how easily a polymer flows when melted, making it a key indicator for material processability. It measures the number of grams of a polymer that flows through a small die over 10 minutes under specific temperature and pressure.
In simple terms, a higher MFI means the material flows more easily, which is useful for processes like thin-wall injection molding. A lower MFI, on the other hand, means the material is thicker and flows more slowly—better for heavy-duty extrusion.
For a deeper look at the science behind MFI and MFR, check out our full guide: Understanding Melt Flow Rate & Index.
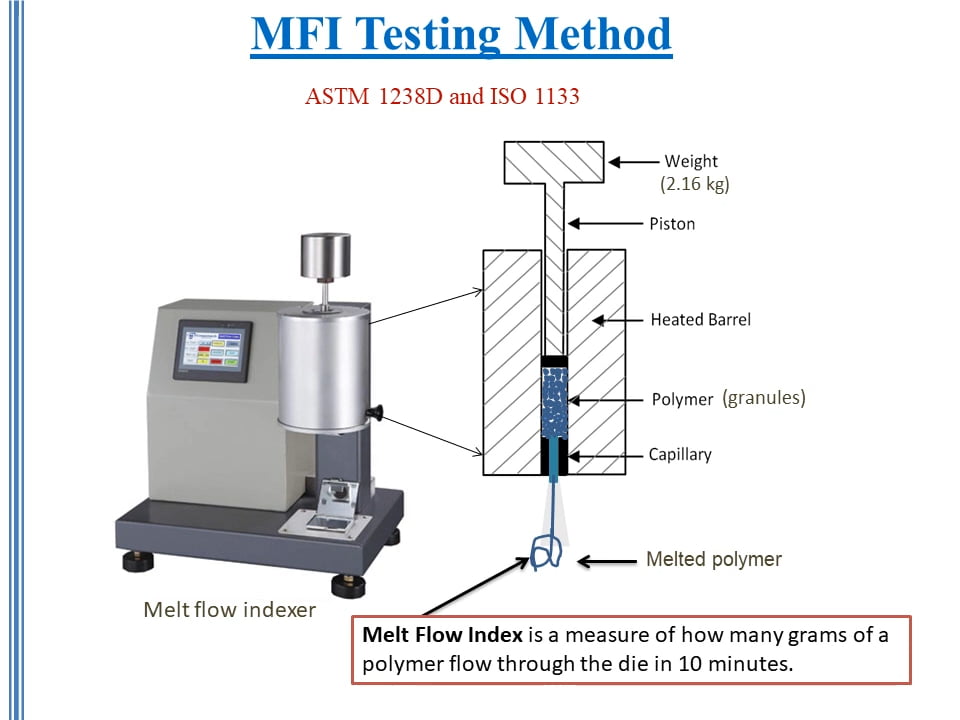
2. Melt Flow Index Table for Common Polymers
If you’re working with polymers, understanding their melt flow index (MFI) is essential. It helps you quickly compare how different plastics behave under heat and pressure—and whether they’re suitable for your specific process.
The table below shows MFI ranges for commonly used polymers, along with their test conditions based on ASTM D1238 or ISO 1133 standards.
Keep in mind: MFI values are not fixed. They can change depending on the grade of the polymer, any additives or fillers, and even the manufacturer’s formulation. That’s why it’s always a good idea to confirm the exact MFI from a trusted supplier when making material decisions.
Use this table as a general reference to compare flowability across plastic types and narrow down options based on your molding or extrusion needs.
Polymer | Typical MFI Range (g/10 min) | Test Conditions (°C, Load) | Common Applications | Limitations |
Low-Density Polyethylene (LDPE) | 0.1–30 | 190°C, 2.16 kg | Flexible films, bags, squeeze bottles | Wide MFI range; lower strength in high-MFI grades |
High-Density Polyethylene (HDPE) | 0.1–3 | 190°C, 2.16 kg | Pipes, containers, caps | Lower MFI increases rigidity but may require higher processing temperatures |
Linear Low-Density Polyethylene (LLDPE) | 0.5–5 | 190°C, 2.16 kg | Stretch films, tough bags | Limited flowability compared to LDPE |
Polypropylene (PP) | 0.5–50 | 230°C, 2.16 kg | Automotive parts, fibers, thin-wall packaging | High-MFI grades may sacrifice impact resistance |
Polystyrene (PS) | 2–20 | 200°C, 5.00 kg | Disposable cutlery, CD cases, housings | Brittle; not suitable for flexible applications |
Polycarbonate (PC) | 3–20 | 300°C, 1.20 kg | Lenses, electronic housings, safety equipment | High processing temperatures; sensitive to moisture |
Nylon (PA6) | 5–50 | 235°C, 2.16 kg | Gears, bearings, under-hood parts | Hygroscopic; MFI affected by moisture content |
Polyethylene Terephthalate (PET) | 5–20 | 280°C, 2.16 kg | Bottles, films, fibers | Requires drying before testing to avoid inconsistent results |
Acrylonitrile Butadiene Styrene (ABS) | 1–50 | 220°C, 10.00 kg | Automotive components, toys, enclosures | MFI varies widely by grade; UV sensitivity |
Polylactic Acid (PLA) | 5–30 | 190°C, 2.16 kg | Biodegradable packaging, 3D printing | Lower thermal stability; degrades at high temperatures |
Key Notes:
- Variability: MFI values are approximate and depend on polymer grade, molecular structure, additives, or supplier formulations. For example, a high-MFI PP for thin-wall molding differs significantly from a low-MFI PP for automotive parts.
- Recycled Polymers: MFI can indicate degradation or contamination in recycled materials. A shift in MFI from the expected range may signal quality issues.
- Testing Standards: Ensure MFI values are compared under identical conditions (e.g., same temperature and load). Consult ASTM D1238 for detailed test procedures.
3. How MFI Values Guide Polymer Selection
The Melt Flow Index (MFI) is a practical tool that helps you pick the right polymer for your production process.
Different plastic processing methods need materials to flow at different rates. For example, injection molding, especially for thin-wall parts like containers or lids, usually requires polymers with high MFI values, around 20–50 g/10 min. These materials flow easily, fill molds quickly, and work well at high speeds.
In contrast, extrusion or blow molding—used to make thick pipes or durable bottles—typically calls for low MFI materials in the range of 0.1–3 g/10 min. These materials have higher viscosity, making them better suited for building strong, consistent shapes without warping or distortion.
But there’s always a trade-off. Higher MFI means better flow, but it can also mean weaker mechanical strength. That’s because polymers that flow too easily often have shorter molecular chains, which can reduce toughness or impact resistance.
On the flip side, lower MFI polymers may be tougher and more durable, but they require higher processing temperatures and pressure.
So, when choosing a material, it’s not just about how easily it flows—it’s about finding the right balance between processability and performance. MFI helps you do that. Whether you’re molding thin film or extruding thick tubing, understanding MFI ensures you get materials that not only fit your machines—but also meet the final product’s strength, look, and durability requirements.
4. MFI Variations Across Polymer Grades and Applications
Not all polymers with the same name behave the same way. Even within one material family—like polyethylene—you’ll find big differences in melt flow index (MFI) depending on the grade, molecular structure, or added ingredients.
Take LDPE vs. LLDPE, for example. Both are forms of polyethylene, but LDPE typically has a higher MFI and more branching in its molecular structure. That makes it more suitable for flexible film and packaging, where easy flow is a priority. On the other hand, LLDPE usually has a lower MFI and better tensile strength, making it great for tougher bags or stretch film.
Additives and fillers can also affect MFI. A polypropylene (PP) used for automotive parts may have a low MFI to enhance stiffness and heat resistance, while another PP grade used for nonwoven fabrics might be highly flowable (MFI > 35) for fast fiber spinning.
This is why it’s essential to look beyond the base polymer name. Suppliers often list MFI on their datasheets, but the number alone doesn’t tell the whole story. Check the test conditions (temperature and load), and always compare MFI values under the same standards.
When in doubt, ask for application-specific grades. A 10 g/10 min PP for injection molding won’t behave the same as a 10 g/10 min PET for film—even if the MFI looks identical. Context matters.
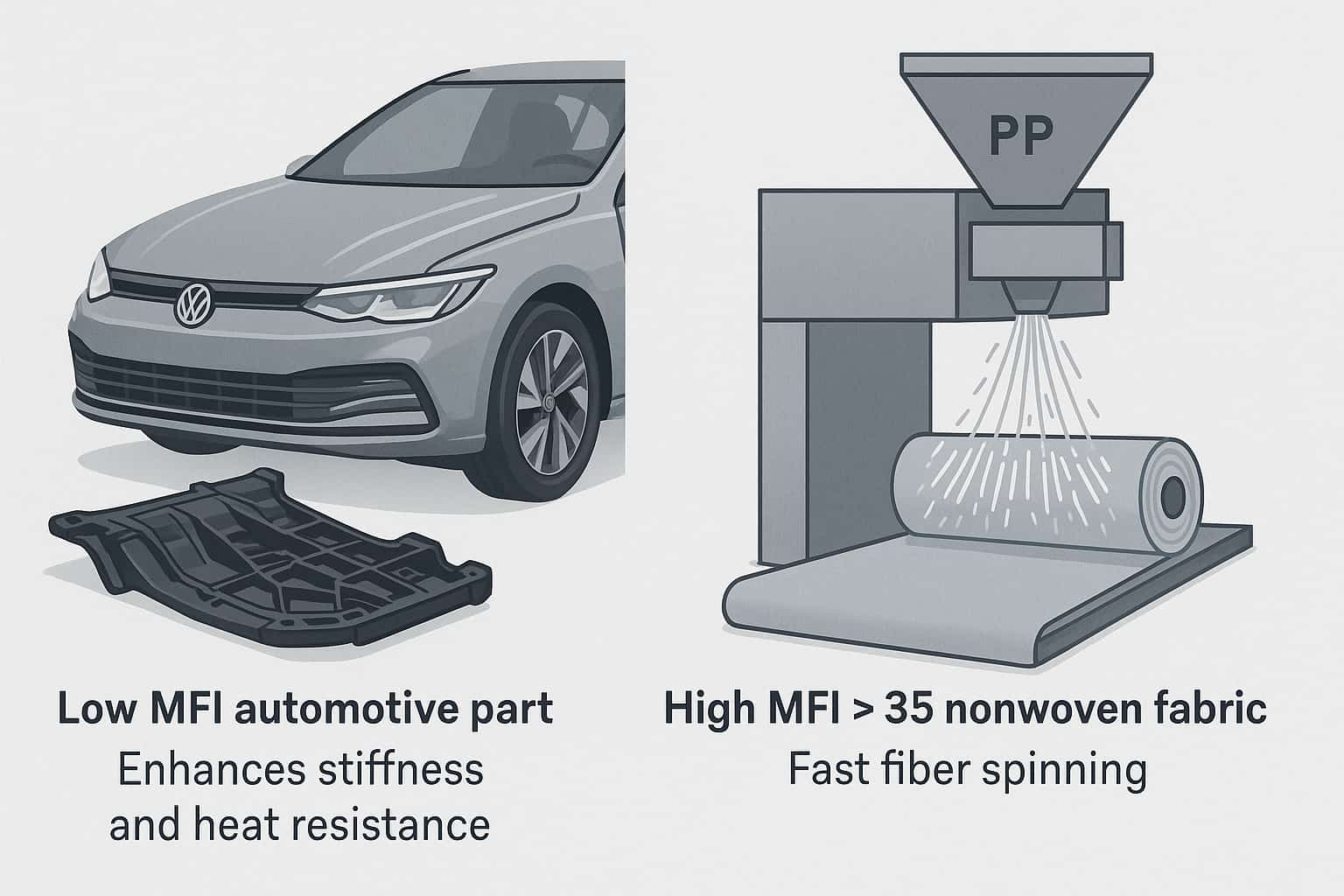
5. Practical Tips for Using MFI Tables in Manufacturing
When using an MFI table to choose a polymer, start with your process. If you’re doing injection molding, look for polymers with higher MFI values—typically above 10 g/10 min—for faster flow into complex molds. If you’re working with extrusion or blow molding, lower MFI values (under 3) often provide better strength and dimensional control.
But don’t stop at the numbers. Always cross-reference MFI values with processing needs and product requirements. For example, a high-MFI material may work well in theory but fall short if the final product requires impact resistance or long-term durability.
Also, check the test conditions listed in the MFI table. A value measured at 190°C, 2.16 kg isn’t the same as one tested at 300°C, 1.2 kg. To compare materials fairly, make sure you’re looking at results based on the same standards—typically ASTM D1238 or ISO 1133.
Finally, don’t rely only on datasheets. Verify MFI in-house when possible, especially for recycled or filled materials. And if you’re sourcing new batches, ask suppliers to confirm test methods. MFI tables give you a great starting point—but consistent quality comes from real-world checks.
6. Frequently Asked Questions About Polymer MFI
- What do MFI values indicate about polymer performance?
MFI shows how easily a polymer melts and flows. Higher MFI means better flow but usually lower strength. Lower MFI indicates tougher material with slower flow—ideal for heavy-duty or structural parts. - How do test conditions affect MFI results in the table?
MFI values depend on temperature and load. A polymer tested at 190°C, 2.16 kg can’t be directly compared to one tested at 300°C, 1.2 kg. Always check the test settings to ensure apples-to-apples comparison. - Why do MFI ranges vary for the same polymer type?
Different grades, additives, or molecular structures affect MFI. For example, LDPE and LLDPE have different branching, resulting in different flow behaviors even though both are polyethylene. - How can MFI tables support recycled polymer evaluation?
MFI helps assess the quality and consistency of recycled plastics. Changes in MFI over time may reveal degradation, contamination, or batch variation—critical for quality control. - What is the difference between MFI and MVR in polymer testing?
MFI measures mass flow (grams), while MVR measures volume flow (cm³). They describe similar behaviors but use different units. MVR is more useful when density differences matter.
Conclusion
The Melt Flow Index (MFI) is a critical tool for understanding polymer flowability, guiding material selection, and ensuring quality in manufacturing processes like injection molding and extrusion. Our comprehensive MFI table for common polymers provides essential data to help manufacturers choose the right materials for specific applications.
For high-quality filler masterbatch to optimize your polymer formulations, EuP Egypt offers reliable solutions tailored to your needs—contact us to learn more. Leverage MFI data to make informed decisions and stay ahead in the dynamic world of polymer processing.
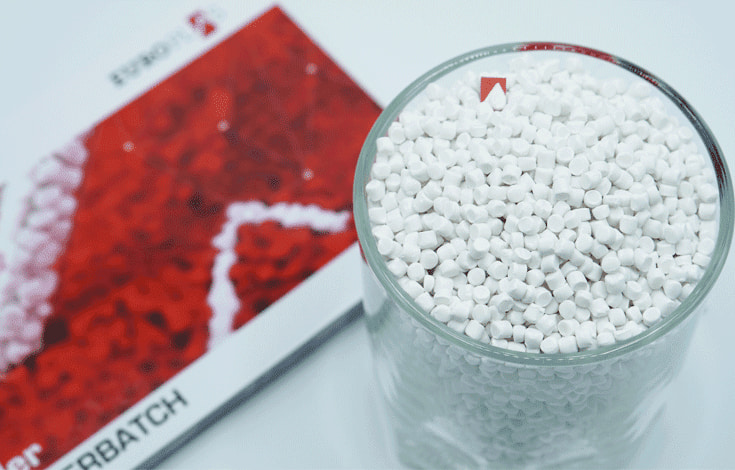