PP Raffia has emerged in the plastic industry as a sustainable material that offers high durability and strength for finished products. The manufacturing process of PP Raffia is quite complicated, requiring manufacturers to learn how to minimize defects. This article will introduce the common issues in PP Raffia production.
1. Understanding PP Raffia in the Plastic Industry
PP raffia (Polypropylene raffia) is a material used in the packaging industry, made from woven polypropylene ribbons. This material is widely utilized for making various items such as PP bags, laminated PP bags, shade nets, FIBC bags, and greenhouse twines.

2. PP Woven Bag’s Manufacturing Process
Woven polypropylene bags (PP woven bags) are commonly used by retailers as ideal alternatives to single-use plastic bags. They have convinced many consumers with their durability, waterproofness, washability, and especially eco-friendliness. These woven bags are great packages for various items such as food, chemical products, or cement.
The manufacturing process of PP woven bags requires many steps and machines, as well as frequent quality controls. Manufacturers use extrusion as the main technique for making these sustainable bags. Below are some steps to turn PP raw materials into finished sustainable PP bags.
- Step 1: PP raw materials are injected into an extruding machine for melting and stretching into a film of the desired thickness. Then, a thermostatic controller cools the plastic film.
- Step 2: Once the extrusion is completed, the plastic strips are wrapped into rolls.
- Step 3: Manufacturers use circular looms to weave polypropylene rolls into flat, tube-shaped threads.
- Step 4: These tubes are customized to achieve the desired colors, patterns, sizes, and shapes according to customer requirements.

3. Common Errors In The PP Raffia Process (And How To Solve Them)
The PP Raffia Process is, in fact, a complicated procedure that requires manufacturers to master all the steps and combine various specialized machines. To enhance performance and ensure the success of any PP Raffia manufacturing project, manufacturers need to learn how to manage defects. There are several common errors that manufacturers should be aware of.
Poorly dispersed filler
One of the main reasons for the poor dispersion of filler is the provision of unqualified products by manufacturers. Other reasons might include substandard raw materials, interrupted production, or unhygienic product equipment.
- Substandard raw materials: Utilizing too much waste plastic or overly moisturized materials can hardly guarantee quality. In this case, make sure to dry the materials before manufacturing.
- Interrupted production: In PP Raffia manufacturing, if the machine is stopped for a long time, it can cause the extruder block to close. The yarn will only return to normal after the machine has been running for a while.
- Unhygienic product equipment: This is a typical issue in manufacturing. Cleaning equipment regularly is crucial for production efficiency.
- Color fading: Color fading refers to the gradual loss or alteration of color in materials over time. This phenomenon can occur due to several environmental factors, such as light exposure, oxidation, humidity, and water exposure.
In this case, manufacturers should keep the following solutions in mind:
- Increasing the use of plastic additives that function as UV stabilizers and antioxidants can help prevent color fading.
- Optimizing manufacturing conditions and storing products away from direct sunlight, high temperatures, and moisture can help preserve color integrity.

Film stripes
Film stripes usually occur after passing through the cooling water tank. Several factors can cause this issue:
- The plastic is not extruded evenly throughout the mold due to insufficient plastic flow pressure.
- Inappropriate mixing of material composition can affect the plastic flow.
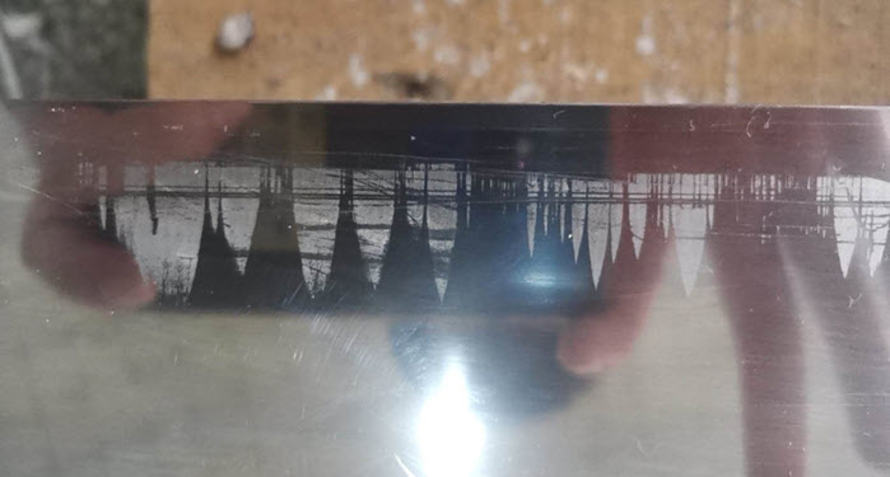
Film carries water
After pulling up the film from the cooling water tank, some water may be pulled along. This defect can decrease the strength and elongation of the yarn, as the water will affect the yarn orientation when it is drawn to the streaming table.
Here are some ways to handle this issue:
- Increasing the utilization of filler during spinning can enhance the smoothness of the process.
- Adding plastic additives that contain hydrophilic functions to the production.
- Equipping the spinning machine with auxiliary systems, including water-absorbing rod systems and wipers.
Dust
Dust is a phenomenon where white powder appears at the contact points with the manufacturing devices. In fact, this issue is inevitable during production. The amount of dust generated depends on the manufacturing conditions and the mixing ratio of raw materials.

Machine and equipment problems
In addition, some common errors in the PP raffia process can be caused by machine and equipment problems, including:
- Inconsistent Extrusion: Worn-out or improperly calibrated extruders can lead to inconsistency in thread thickness and quality.
- Mechanical Wear and Tear: A common reason for the inefficient operation of machinery is the worn-out condition of components such as barrels, screws, and rollers. To avoid this issue, it is necessary to implement regular preventive maintenance for inspecting and replacing broken components.
4. Conclusion
PP Raffia is likely to gain more popularity in the plastic product market as consumers seek more eco-friendly and sustainable products. Mastering manufacturing processes and understanding production defects can help manufacturers increase efficiency while saving time and costs.
5. About EuP Egypt’s PP Products
EuP Egypt is a member of EuP, one of the largest masterbatch manufacturers worldwide. PP filler masterbatch is among our flagship products and helps us gain customer interest. This filler masterbatch offers many advantages in plastic production, including:
- Enhancing mechanical properties: It improves hardness, elongation, flexibility, and stretchability of the final products, contributing to better quality and performance.
- Accelerating energy efficiency: The excellent thermal properties of PP filler masterbatch contribute to energy savings during production, further reducing overall manufacturing costs.
- Improving productivity: The material’s ability to cool quickly accelerates the extrusion process, boosting productivity by decreasing processing time.
- Ensuring dimensional stability: Incorporating PP filler masterbatch in the production process helps minimize shrinkage, retaining the end products’ intended dimensions and shapes.
Contact us for more information about this sustainable filler masterbatch!