Reducing production costs without compromising quality is one of the primary concerns of many PP jumbo bag manufacturers. The rising cost of raw materials, especially polypropylene, has made this challenge more urgent. The incorporation of PP filler masterbatch allows manufacturers to make significant cost savings while maintaining bag strength and performance. This new development, which combines economy and quality seamlessly, is revolutionizing the PP jumbo bag industry. Let’s discover right below!
1. Cost Challenges in PP Jumbo Bag Production

PP jumbo bags play an essential role across various sectors, including agriculture, construction, and food industry. Along with the high demand for PP jumbo bags, one of the challenges for manufacturers is that production costs are gradually increasing.
Polypropylene (PP) is the main raw material for PP jumbo bags. The increasing price of this raw material is also the main cause of cost challenges for the production process. Some of the main reasons are the fluctuating crude oil prices along with the increasing demand from the market. This is a warning for manufacturers to tightly control costs to provide quality products at affordable prices.
The current challenge of PP jumbo bag production costs is considered to have a profound impact on a variety of fields. Increased packaging costs mean that the final product price will also fluctuate. Finding optimal solutions to balance production costs and maintain stable product prices is one of the necessary tasks right now!
2. Reduce PP Jumbo Bags Production Costs with PP Filler Masterbatch
Finding solutions to save production costs of PP jumbo bags is a concern of most manufacturers. PP filler masterbatch is being evaluated as one of the ideal options for this context. The impact of PP filler masterbatch is affirmed to be a turning point for manufacturers who want to maintain profits and meet market demands.
2.1. What is PP Filler Masterbatch
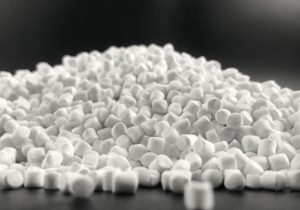
PP filler masterbatch is a mixture combining calcium carbonate (CaCO3), PP resin and some other functional additives. Currently, this material is very popular in combination with virgin polypropylene in the process of PP jumbo bag production.
By replacing a part of virgin PP plastic with filler masterbatch, manufacturers can significantly reduce the cost of expensive raw materials. In addition, the use of filler masterbatch also helps facilitate the adjustment of desired product properties to suit different operating environments.
2.2. Benefits Of Using PP Filler Masterbatch For PP Jumbo Bag Production

- Significant Cost Savings
In any manufacturing industry, raw material costs are a major concern in determining production costs. Having an affordable PP Filler Masterbatch raw material solution is a key business’s competitiveness. Costs are significantly optimized when replacing a portion of expensive virgin polypropylene with calcium carbonate and additives. The savings in raw material costs also allow for competitive pricing and improved profit margins for a PP jumbo bag in the market.
- Improved product durability
A stronger PP jumbo bag will help ensure more efficient and safe storage and transportation. The calcium carbonate component in PP filler masterbatch increases the tensile strength and durability of PP jumbo bags to meet the application needs in cases where heavy loads need to be handled. In the construction industry, cement or sand jumbo bags are also favored thanks to their durability.
- Better heat resistance
PP Filler Masterbatch provides a PP jumbo bag with improved thermal stability to ensure that the bag maintains its structural integrity at high or low temperatures. This is especially important for heat-sensitive products such as those exposed to sunlight for long periods of time or in cold environments.
- Environmentally friendly production
Creating a sustainable material to meet the requirements of the green industry is always the top goal of most manufacturing industries in the current context. PP Filler Masterbatch with the ability to reduce dependence on virgin polypropylene plastic, reducing the environmental footprint of the production process.
Calcium carbonate in PP Filler Masterbatch is an abundant source of raw materials and recyclable. PP jumbo bags will increasingly occupy a position in the hearts of consumers when bringing a message of environmental protection.
- Improved printability
Appearance is crucial in high-quality PP jumbo bag production. The role of PP Filler Masterbatch is to increase the surface finish of the jumbo bag, facilitating the printing process. A superior print quality enables stronger branding and marketing, helping to win the trust of consumers.
3. Optimum Filler Masterbatch Loading in PP Jumbo Bags
Proper PP filler masterbatch loading is crucial for cost efficiency and value addition in jumbo bag production. Both overloading and underloading can lead to inefficiency and higher costs. The right loading will bring worthy benefits to the manufacturer. Check out these helpful suggestions below:

3.1. Understanding of factors
The optimal quantity of filler masterbatch for PP jumbo bag products will depend on several factors given below:
- Target Application: The packaging bags used by high-damage applications are to be produced accordingly. Construction material packing generally falls under these criteria, whereas agricultural and food industries have another formula.
- Desired Properties: Depending on the operating environment or the object that needs to be contained inside, there are different adjustments to the filler masterbatch. This helps ensure that consumers have the best experience for a range of needs.
- Compatibility with PP Resin: The grade of polypropylene resin that would be used determines the amount of filler masterbatch that can effectively be incorporated.
- Processing Conditions: Several factors during processing can directly impact the quality of a PP jumbo bag. The temperature of extrusion, screw design, and blending equipment will affect dispersion of the filler masterbatch.
3.2. Recommended Loading Levels
In general, PP filler masterbatch loading falls in a range from 10% to 30% of the total material blend. This is further referenced below:
- Low Loading (10-15%): In this range, one gets very high tensile strength, suitable for applications such as food-grade PP jumbo bag. It keeps the bag light and flexible while maintaining the rigid safety standards of the products.
- Moderate Loading (15-25%): This is applied to general-purpose bags used in agriculture or light industry. It reaches a compromise between cost reduction and the maintenance of basic properties.
- High Loading (25-30%): Applied in applications that are not critical, where the saving of costs is more important than mechanical properties.
4. EuP Egypt – Your Trusted PP Filler Masterbatch Partner
EuP Egypt is proud to be a key member of EuP Group, a world leader in filler masterbatch solutions. With 17 years of extensive experience and modern facilities, we are honored to be a trusted partner for plastic manufacturers worldwide.
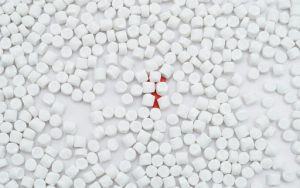
PP filler masterbatch is meticulously designed to meet the comprehensive requirements of PP jumbo bag production and many other product lines. This innovative material combines high-quality CaCO3 powder, PP resin and advanced additives, ensuring superior performance for the targeted product.
The main mission of EuP Egypt’s PP filler masterbatch is to promote cost-effective production by replacing a large portion of expensive virgin PP resin, improving mechanical properties and improving processing efficiency through optimized thermal properties.
5. Case study
Case Study: Optimizing the Cost of PP Jumbo Bag Production in Egypt

- Background:
Egypt is a country that has a high demand on PP jumbo bags for bulk transportation. However, with the rising prices of raw materials – especially for polypropylene – manufacturers are finding it increasingly difficult to produce at competitive prices without compromising the durability and quality of the jumbo bags.
This is the case of a PP jumbo bag manufacturer in Alexandria (Egypt), which incurs high production costs because it relies 100% on virgin PP. This situation reduces their price competitiveness and profitability, especially in the international market, where cost efficiency is one of the key differentiators.
- EuP Egypt’s Solution:
The manufacturer contacted EuP Egypt and we proposed using EFPP filler masterbatch and adding 20% PP Filler Masterbatch to the production.
- Result:
By using PP Filler Masterbatch in production, the Egyptian manufacturer achieved the following expected results. This process reduced the cost of virgin PP raw material by 15%. The company saved a large amount of production costs, helping them price their products more competitively in the market. The surface quality of the bag is improved, increasing branding opportunities – a very important factor for export markets. Reducing reliance on virgin plastic meets the growing global emphasis on sustainable manufacturing practices.
6. Conclusion
In conclusion, the addition of PP filler masterbatch to PP jumbo bag production will be a game-changer for manufacturers who are facing rising material costs. This solution not only saves on the use of virgin PP resin, helping to cut costs, but also maintains its key performance characteristics such as strength, durability, and printability.
With the ever-evolving manufacturing techniques, it is expected that there will be many great improvements in PP filler masterbatch to make PP jumbo bag production more sustainable.
Contact us now to access the top quality PP filler masterbatch for your project!