Thermoforming has revolutionized plastic manufacturing by turning polymer sheets into functional, high-quality products with precision and quick speed. Its impact spans industries, producing everything from food containers to medical equipment. This article will dive into the fascinating world of thermoforming, explaining how it works, its diverse applications, and why it has become a preferred solution for manufacturers worldwide.
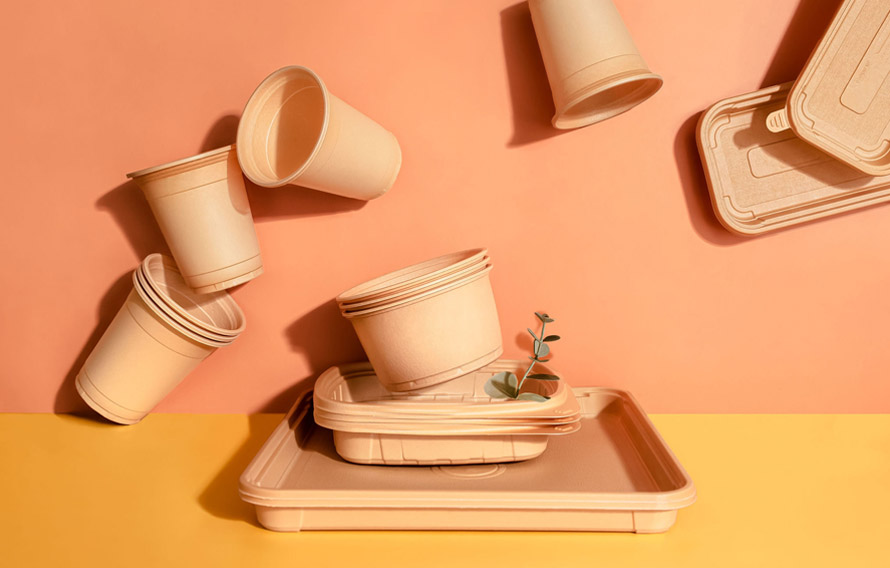
1. What Is Thermoforming?
Thermoforming is a plastic manufacturing technique where a sheet of plastic is heated to a flexible temperature, shaped using a mold, and then trimmed into its final form. For thin materials, often referred to as “film,” the sheet is heated and stretched over or into a mold, then cooled to set its shape. A basic example of this is vacuum forming, which involves using a vacuum to shape heated plastic over a mold, commonly used for prototypes and small batches. For large-scale applications, high-speed machines handle continuous production, forming and trimming thousands of items per hour.
This process is distinct from other plastic molding techniques like injection or blow molding. Thin-gauge thermoforming is commonly used for creating disposable items such as cups, lids, trays, and clamshell packaging, widely seen in food, medical, and retail industries. Meanwhile, thick-gauge thermoforming is employed for durable items like vehicle panels, refrigerator liners, and utility components.
Sustainability is a key focus for many thermoforming companies. Scrap and waste materials from the process are often recycled on-site or sold to reprocessors, with leftover plastic frequently turned back into sheets for reuse. This recycling approach not only reduces waste but also makes thermoforming an increasingly environmentally responsible option in plastic manufacturing.

2. How Thermoforming Process Works?
The thermoforming process involves several key stages, each critical for shaping thermoplastic materials into desired forms.
2.1. Material Selection: Tailoring Performance to Application
The first crucial step involves selecting the most appropriate thermoplastic material for the desired application. Factors like strength, flexibility, chemical resistance, and heat tolerance are all considered during this material selection phase. Common thermoplastics used in thermoforming include ABS, PETG, HIPS, and polystyrene, etc. Each offering distinct properties for specific end-use requirements.
2.2. Precise Heating: Achieving Optimal Formability
Once the material is chosen, the plastic sheet undergoes a controlled heating process. The sheet is carefully heated within a designated temperature range to achieve a pliable state. This precise heating ensures optimal formability while minimizing the risk of material degradation or burning. Modern thermoforming machines utilize advanced temperature control systems to maintain consistent and uniform heating throughout the sheet.
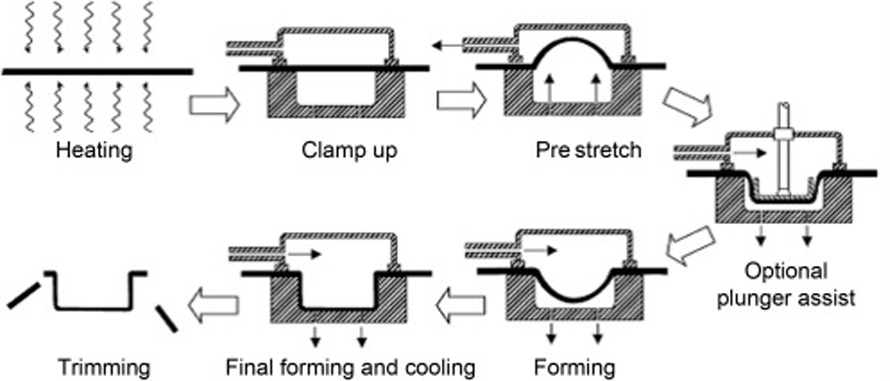
2.3. Shaping the Plastic: From Sheet to Three-Dimensional Form
The heated plastic sheet is then shaped into the desired three-dimensional form using a pre-designed mold. This shaping process can be achieved through various techniques, including:
- Vacuum Forming: A vacuum is applied to draw the softened plastic sheet tightly onto the mold cavity, creating the desired shape.
- Pressure Forming: Compressed air is used to force the heated plastic sheet onto the mold surface, replicating the mold’s contours.
- Mechanical Forming: Mechanically actuated tools manipulate the softened plastic sheet into the desired form within the mold.
- Drape Forming: In drape forming, a heated plastic sheet is draped over a mandrel with a specific shape. The sheet conforms to the mandrel’s shape, creating parts with consistent thickness and minimal stress points.
- Matched Mold Forming: This technique utilizes both a male and female mold to create highly accurate and detailed parts. The heated plastic sheet is placed between the two molds, and pressure is applied to form the desired shape.
- Twin Sheet Forming: This process involves forming two heated plastic sheets simultaneously and then joining them together to create hollow or multi-walled products. This technique is commonly used for products like food containers and beverage cups.
- Billow Forming: Billow forming is a free-form technique where a heated plastic sheet is inflated with air to create a desired shape without the use of a traditional mold. This method is often used to produce unique shapes and custom designs.
2.4. Trimming and Finishing: The Final Touches
After the plastic sheet has cooled and solidified within the mold, the formed part is carefully trimmed to remove any excess material. This trimming process ensures precise dimensions and a clean aesthetic for the final product. Depending on the application, additional finishing steps like sanding, polishing, or hole punching might be employed to achieve the desired final product specifications.
3. Plastic Materials Used In Thermoforming
Plastic materials used in thermoforming are chosen for their unique properties, such as durability, flexibility, or impact resistance, to suit specific industrial applications. Each material offers distinct advantages, enabling versatility in products.
- Polypropylene (PP): Known for its excellent chemical resistance, high strength and flexibility, PP is widely used in food packaging and automotive applications.
- Acrylonitrile Butadiene Styrene (ABS): This versatile material provides a good balance of strength, impact resistance, and formability, making it suitable for a wide range of products like electronic protective cases, domestic appliances and automotive parts, etc.
- High Impact Polystyrene (HIPS): Cost-effective and known for its ease of forming, HIPS is a popular choice for disposable packaging and blister packs.
- High-Density Polyethylene (HDPE): Known for its superior strength and chemical resistance, HDPE is often used for industrial components and heavy-duty packaging.
- Polyvinyl Chloride (PVC): PVC offers a balance of strength, affordability, chemical resistance, and good electrical insulator making it suitable for various applications depending on the specific formulation.
- Polystyrene (PS): A cost-effective and transparent material, PS is often used for disposable packaging and displays. (Note: Limited heat resistance compared to other options)
- Polyethylene Terephthalate (PET): PET offers excellent clarity, good chemical resistance, and barrier properties, making it ideal for food packaging, water bottles, and medical device applications.
- Low-Density Polyethylene (LDPE): This flexible thermoplastic material offers good chemical and UV rays resistance, impact strength, suitable for packaging applications requiring flexibility.
- Polycarbonate (PC): Known for its exceptional strength, impact resistance, and clarity, PC is often used for demanding applications like safety shields, optical applications and medical devices.
- Cellulose Acetate: Biodegradable and lightweight, this material is frequently employed in eco-friendly packaging and films
- Polymethyl methacrylate (PMMA): PMMA boasts exceptional clarity and scratch resistance, making it a preferred choice for vehicle headlamps, produce lenses, or transparent packaging.

4. What Are The Advantages And Disadvantages Of Thermoforming?
4.1. Advantages Of Thermoforming
Thermoforming offers a compelling array of benefits for manufacturers across diverse industries. Here’s a breakdown of its key advantages:
- Versatility and Adaptability: Thermoforming can accommodate a wide range of plastic materials and produce parts with varying thicknesses and intricate shapes. This flexibility allows for the creation of products for numerous applications.
- Large scale project: Thermoforming offers a unique advantage over other plastic molding processes by accommodating large-scale projects. It is unlike many plastic molding techniques, which are often limited to smaller items.
- Cost-Effectiveness: The simplicity of the thermoforming process and the availability of skilled labor make it a cost-effective option for many manufacturers.
- Suitable with almost all types of plastic: Its versatility allows it to work with a wide range of thermoplastic materials, making it a flexible solution for various applications.
- Fast Production Speeds: Thermoforming processes are often automated and efficient, allowing for high production rates. It enables the production of high-quality products in a relatively short time frame. This translates to faster turnaround times and reduced overall production costs.
- Durable and Functional Products: Thermoforming can create robust and functional parts with good dimensional stability. The process can also incorporate features such as hinges and integrated components, further enhancing product functionality.
- Aesthetic Appeal: Thermoforming allows for the use of colored and paintable plastics, enabling the creation of visually appealing products that meet specific aesthetic requirements.
4.2. Disadvantages Of Thermoforming
Thermoforming, while highly versatile, has certain limitations that can affect its applications. Understanding these disadvantages is essential for choosing the most suitable manufacturing process.
- Limited to Thin-Walled Parts: While thick-gauge thermoforming exists, the process is primarily suited for producing parts with relatively thin walls. This may restrict its application in situations requiring thick, highly rigid components.
- Geometric Constraints: Certain product geometries, particularly those with undercuts or complex internal features, may be challenging or impossible to achieve using thermoforming techniques.
- Potential for Uneven Material Distribution: During the heating and forming stages, there’s a possibility of uneven material distribution. This can impact product strength and require careful process optimization.
- A bit more expensive: Thermoforming tends to be more costly than alternatives like injection molding.
5. What Are The Main Applications Of Thermoforming?
Thermoforming serves a wide range of industries due to its versatility and efficiency. Here are its primary applications:
- Packaging: Widely used for creating food-grade containers, trays, clamshells, and blister packs due to its hygienic properties and cost-effectiveness
- Household Items: Thermoforming is extensively used to create various household products, including storage solutions, trays, and toys. Items produced through this process are lightweight, easy to maintain, and safe for everyday use.
- Automotive: Ideal for producing lightweight yet durable components such as interior panels, bumpers, and trunk liners
- Agriculture: Thermoforming is widely utilized in agriculture to produce durable plastic items like plant pots and greenhouse components, designed to withstand environmental stress and protect crops effectively.
- Healthcare: Thermoforming enables the production of custom trays, medical device housings, and pharmaceutical blister packs, meeting stringent safety and sterility standards
- Aerospace: It facilitates the manufacture of lightweight structural parts and cabin components that meet strict durability and weight specifications
- Retail and Displays: Used to create point-of-purchase displays, signage, and protective packaging for consumer goods
- Construction: Thermoformed materials are employed in applications like roofing panels, window wells, and wall coverings due to their resilience and customizability
- Industrial Equipment: This process is used to fabricate machine housings, panels, and protective covers for heavy equipment.

6. FAQs about Thermoforming
What are common quality issues in thermoforming?
Quality challenges in thermoforming often involve irregular wall thickness, surface imperfections such as scratches or bubbles, and deformation during cooling, which can affect the functionality and appearance of the product.
How environmentally friendly is thermoforming?
Thermoforming offers some eco-friendly benefits, such as the potential for recycling and the use of low-energy production methods. However, its environmental friendliness is limited by material choices and the generation of waste during the manufacturing process, which may not always be efficiently reused
What are the latest trends in thermoforming technology?
Recent trends in thermoforming technology highlight several advancements that improve production efficiency and open up new possibilities for manufacturing. One notable trend is the integration of digitalization and automation, which enhances real-time monitoring, predictive maintenance, and efficiency. Additionally, the use of 3D printing for mold prototyping has reduced lead times and allowed for quicker design iterations
7. Conclusion
Thermoforming, a versatile plastic manufacturing process, is widely utilized across industries, offering cost-effective production for a range of applications, from packaging to automotive parts. As we conclude our comprehensive guide, it’s clear that this process continues to evolve, with advancements in technology enhancing both efficiency and sustainability.
EuP Egypt has embraced these developments, offering tailored solutions in the form of filler masterbatches, color additives, and bioplastic compounds, which contribute to enhancing product durability, aesthetics, and environmental responsibility. Through innovations in materials and production techniques, EuP Egypt is helping manufacturers meet the growing demand for high-performance, eco-friendly plastic products across various sectors, including packaging, agriculture, and home entertainment, etc.
For further inquiries or to explore how EuP Egypt can support your specific needs, contact us today.